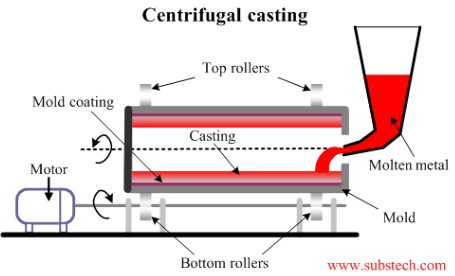
centrifugal casting machine
Centrifugal Casting: In centrifugal casting, a permanent mold is rotated about its axis at high speeds (300 to 3000 rpm) as the molten metal is poured. The molten metal is centrifugally thrown towards the inside mold wall, where it solidifies after cooling. The casting is usually a fine grain casting with a very fine-grained outer diameter, which is resistant to atmospheric corrosion, a typical situation with pipes. The inside diameter has more impurities and inclusions, which can be machined away.
Only cylindrical shapes can be produced with this process. Size limits are upto 3 m (10 feet) diameter and 15 m (50 feet) length. Wall thickness can be 2.5 mm to 125 mm (0.1 - 5.0 in). The tolerances that can be held on the OD can be as good as 2.5 mm (0.1 in) and on the ID can be 3.8 mm (0.15 in). The surface finish ranges from 2.5 mm to 12.5 mm (0.1 - 0.5 in) rms.
Typical materials that can be cast with this process are iron, steel, stainless steels, and alloys of aluminum, copper and nickel. Two materials can be cast by introducing a second material during the process. Typical parts made by this process are pipes, boilers, pressure vessels, flywheels, cylinder liners and other parts that are axi-symmetric.
Semi-Centrifugal Casting: The molds used can be permanent or expendable, can be stacked as necessary. The rotational speeds are lower than those used in centrifugal casting. The center axis of the part has inclusion defects as well as porosity and thus is suitable only for parts where this can be machined away. This process is used for making wheels, nozzles and similar parts where the axis of the part is removed by subsequent machining.
Centrifuging: Centrifuging is used for forcing metal from a central axis of the equipment into individual mold cavities that are placed on the circumference. This provides a means of increasing the filling pressure within each mold and allows for reproduction of intricate details. This method is often used for the pouring of investment casting pattern.
|