¾Õ¿¡¼ Ãë±ÞÇÑ »çÇü(Þãúþ)¿¡¼¿Í´Â ´Þ¸® ÁÖÇü ³»ÀÇ ¿ëÅÁ¿¡ ¾Ð·ÂÀ» °¡Çϰųª Á¤¹ÐÁÖÇü¿¡¼ÀÇ Á¤µµ°¡ ³ôÀº ÁÖ¹°À» ¾ò´Â ÁÖÁ¶¹ýÀ»
ÅëÅÐ¾î Æ¯¼öÁÖÁ¶¹ýÀ̶ó ÇÏ¿© º» Àå¿¡¼ ´Ù·é´Ù. ¿ëÅÁ¿¡ ¾Ð·ÂÀ» °¡ÇÏ´Â ¹æ¹ý¿¡ µû¶ó ¿ø½ÉÁÖÁ¶¹ý°ú die casting ¹ýÀÌ ÀÖÀ¸¸ç,
¿ø½ÉÁÖÁ¶¹ý°ú die casting ¹ý¿¡¼´Â ÁÖÇüÀÌ ±Ý¼ÓÀ¸·Î µÇ¾î ÀÖ¾î ¹Ýº¹ÇÏ¿© »ç¿ëÇÒ ¼ö ÀÖ´Ù´Â Àǹ̿¡¼ À̵éÀ»
¿µ±¸ÁÖÇüÁÖÁ¶¹ý(çµÎùñÑúþñÑðãÛö; perminent-mold casting process)À̶ó°í ÇÑ´Ù.
Á¤¹ÐÁÖÁ¶¹ý¿¡´Â ÁÖÇüÀÇ Á¦ÀÛ ¹æ¹ý¿¡ µû¶ó shell molding ¹ý, investment molding ¹ý ¹×
CO2¹ý µîÀÌ ÀÖ°í, ÀÌ ¹Û¿¡µµ Áø°øÁÖÁ¶¹ý°ú ¿¬¼ÓÁÖÁ¶¹ý µîÀÌ ÀÖ´Ù.
-
ÁÖö°ü ¿Ï¼ºÇ°À» º¸¿©ÁØ´Ù.
|
¿ø½ÉÁÖÁ¶°úÁ¤À» º¸¿©ÁØ´Ù.
|
ÁÖö°üÀ» ¼ö¾Ð½ÃÇèÇÑ´Ù.
|
ÁÖö°üÀÇ ¹æ½Ä(ÛÁãÚ)À» À§ÇÏ¿© ³»¸é¿¡ cement mortarÀ» liningÇÑ´Ù.
|
-
>
¼öÁ÷½Ä ¿ø½ÉÁÖÁ¶±â
|
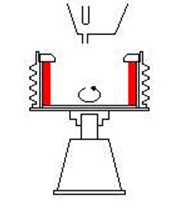
¼öÁ÷½Ä ¿ø½ÉÁÖÁ¶±â
|
ÁÖÇüÀç·á¿¡ µû¶ó ¿ëÅÁÀÌ ±ÝÇüº®°ú Á÷Á¢ Á¢ÃËÇÏ´Â ±ÝÇü°ú ±ÝÇü ³»º®¿¡ »çÃþ(Þãöµ)À» µÎ¾î ¿ëÅÁÀÌ »çÃþ°ú Á¢ÃËÇÏ´Â
»çÇüÀÌ ÀÖ´Ù. ±ÝÇüÀº ÁÖö, ÁÖ°, Ư¼ö°À¸·Î µÇ¾î ÀÖ°í, ÁÖÇüÀÇ ¿Âµµ°¡ ³·À¸¸é ÁÖ¹°ÀÇ ¿ÜÃøÀÌ ¹é¼±È(ÛÜàÕûù)µÇ´Â
°æÇâÀÌ ÀÖÀ¸¹Ç·Î 200 ~ 300¡É Á¤µµ·Î ¿¹¿ÇÏ´Â ¼ö°¡ ÀÖ´Ù.
´ëÇü ÁÖ¹°ÀÇ ÁÖÁ¶¿¡¼´Â ÁÖÇüÀÌ ÆÄ±«µÉ ¿°·Á°¡ ÀÖÀ¸¹Ç·Î ÁÖÇüÀÇ ¿Üº®À» ¼ö³ÃÇÒ Çʿ䰡 ÀÖ´Ù. ÁÖÇü°ú ¿ëÅÁ »çÀÌ¿¡
»çÃþ(Þãöµ)À» µÎ´Â »çÇü¿¡¼´Â ¿ø½É·Â¿¡ ÀÇÇÏ¿© »çÃþÀÌ ÆÄ±«µÇÁö ¾Êµµ·Ï ¼®¸é µîÀ» È¥ÇÕÇÏ¿© Á¦ÀÛÇϰí,
ö°ü ³»º®¿¡ ¿äö(èêôÈ)À» µÎ¾î ÁÖÇü»çÀÇ ºÎÂøÀ» µ½´Â´Ù.
[1-1] ¼öÆò½Ä
ȸÀü¼ö°¡ Ä¿Áö¸é Áß½ÉÂ÷´Â ÀÛ¾ÆÁö³ª, ¥ø¸¦ ³Ê¹« Å©°Ô ÇÏ¸é ¿ø½É·ÂÀÌ Å©°Ô µÇ¾î ÀÀ°í Á÷ÈÄÀÇ ¾àÇÑ »óÅ¿¡¼
¿øÅë¿¡ ³Ê¹« Å« ÀÎÀå·ÂÀÌ ÀÛ¿ëÇÏ¿© crackÀÌ »ý±æ ¿°·Á°¡ ÀÖ°í, e°¡ Å©¸é(¥ø°¡ ÀÛÀ¸¸é) ȸÀüÇÒ ¶§¸¶´Ù
¿ëÅÁÀÌ ±³¶õµÇ°í ȸÀüµµ ºÒ±ÕÇüÇÏ°Ô µÇ¹Ç·Î ȸÀü¼ö´Â G number,
[1-2] ¼öÁ÷½Ä

-
|
¼öÁ÷½Ä ¿ø½ÉÁÖÁ¶±â ¢Ð
|
À½ÄÀ¸·Î ºÎÅÍ ÁÖ¹° ³»¸éÀº Æ÷¹°¼±À» ÀÌ·ç´Â °ÍÀ» ¾Ë ¼ö ÀÖÀ¸¸ç, ÁÖÇüÀÇ Á÷°æÀº °íÁ¤µÇ¾î ÀÖ´Â µ¥ y°¡ Áõ°¡Çϸé x°¡ Áõ°¡ÇϹǷÎ
ÁÖ¹°Àº À§·Î °¥¼ö·Ï ¾ã¾ÆÁø´Ù. ½ÇÁ¦·Î´Â Æ÷¹°¼±ÀÇ Á¤Á¡À¸·ÎºÎÅÍ ¶³¾îÁø ÀÏÁ¤±æÀÌÀÇ ºÎºÐÀ» »ç¿ëÇϸç, À̶§
ÀúºÎ(î¼Ý»)ÀÇ ³»°æ r©û(cm), »óºÎ(߾ݻ)ÀÇ ³»°æ r©ü(cm)¿Í ¿øÅëÀÇ ±æÀÌ L(cm)°úÀÇ °ü°è´Â
-
À½Ä¿¡¼ ÁÖ¹°Á¦Ç°ÀÇ ¾ç´ÜÀÇ ¹ÝÁö¸§ r©û, r©ü¿Í ±æÀÌ LÀ» ¾Ë¸é ÇÊ¿äÇÑ È¸Àü¼ö N(rpm)À» °è»êÇÒ ¼ö ÀÖ´Ù.
º¸Ãæ(100KB, 1¸Å)(¿ø½ÉÁÖÁ¶¹ýÀÇ °è»ê¿¹Á¦)
[2] die casting ¢Ð
Á¤¹ÐÇÑ ±Ý¼ÓÁÖÇü¿¡ °í¾Ð, °í¼ÓÀ¸·Î ¿ëÅÁÀ» ÁÖÀÔÇϰí ÀÀ°íÁß ¾Ð·ÂÀ» À¯ÁöÇÏ¿© ÁÖ¹°À» ¾ò´Â ÁÖÁ¶¹ýÀ¸·Î¼,
ÁÖ¹°Àç·á¿¡´Â Al ÇÕ±Ý, Zn ÇÕ±Ý, Sn ÇÕ±Ý µîÀÌ ÀÖÀ¸¸ç,
¢Ñ Á¦Ç°¿¡´Â
ÀÚµ¿Â÷ ºÎǰ, Àü±â±â±â, Åë½Å±â±â ¿ëǰ, ±âŸ ÀÏ¿ëǰ µîÀÌ ÀÖ´Ù.
Ư¡À» µé¸é
-
ÀåÁ¡
- Á¤µµ°¡ ³ô°í ÁÖ¹°Ç¥¸éÀÌ ±ú²ýÇÏ¿© ´ÙµëÁú ÀÛ¾÷À» ÁÙÀÏ ¼ö ÀÖ´Ù.
- Á¶Á÷ÀÌ Ä¡¹ÐÇÏ¿© °µµ°¡ Å©´Ù.
- ¾ãÀº ÁÖ¹°ÀÇ ÁÖÁ¶°¡ °¡´ÉÇÏ¿© Á¦Ç°À» °æ·®È(ÌîÕáûù)ÇÒ ¼ö ÀÖ´Ù.
- ÁÖÁ¶°¡ ºü¸£±â ¶§¹®¿¡ ´Ù·® »ý»êÀ¸·Î½á ´Ü°¡¸¦ ÁÙÀÏ ¼ö ÀÖ´Ù.
-
´ÜÁ¡
- Àåºñ¿Í die Á¦ÀÛºñ°¡ °í°¡À̱⠶§¹®¿¡ ¼Ò·® »ý»ê¿¡ ºÎÀûÇÕÇÏ´Ù.
- dieÀÇ ³»¿°µµ ¶§¹®¿¡ ¿ëÀ¶Á¡ÀÌ ³·Àº ºñö±Ý¼Ó¿¡ Á¦ÇѵȴÙ.
- ¼ÒÇüÁ¦Ç°¿¡ ±¹ÇÑÇÑ´Ù.
die¿¡ °¡¾ÐÁÖÀÔÀ» Çϱâ À§ÇÑ die casting machineÀÌ ÇÊ¿äÇϸç, °¡¾Ð½ÇÀÇ ±¸µ¿¹æ½Ä¿¡ µû¶ó ¾ÐÃà°ø±â½Ä, ¼ö¾Ð½Ä, À¯¾Ð½ÄÀÌ ÀÖ°í,
°¢°¢¿¡ ´ëÇÏ¿© ¼öµ¿½Ä°ú ÀÚµ¿½Ä, ¿°¡¾Ð½Ç½Ä(æðÊ¥äâãøãÒ; hot chamber type)°ú ³Ã°¡¾Ð½Ç½Ä(ҲʥäâãøãÒ; cold chamber type)ÀÌ
ÀÖ´Ù.
[2-1] die casting machine
¿°¡¾Ð½Ç½Ä die casting machineÀº ¾Æ·¡ ±×¸²°ú °°ÀÌ ³»¿ÁÖöÁ¦ pot¿¡ ³»¿ÁÖöÁ¦ gooseneck°¡ ÀÖ¾î pot ³»ÀÇ ¿ëÅÁÀÌ
neck¿¡ À¯ÀԵǰí plungerÀÇ ÀÛµ¿À¸·Î neck ³»ÀÇ ºñ±³Àû ¿ëÀ¶Á¡ÀÌ ³·Àº ¾Æ¿¬, ÁÖ¼®, ³³, ¶§·Î´Â magnesium µîÀÇ
±Ý¼Ó ¿ëÅÁÀ» die¿¡ ¾Ð·ù(äâêü)½ÃÄÑ ÁÖÁ¶ÇÏ´Â ÁÖÁ¶±âÀÌ´Ù. ¿ëÅÁ¿¡ ÀÛ¿ëÇÏ´Â °¡¾Ð·ÂÀº 50~200kg/cm©÷À̸ç, »ý»ê´É·üÀº ½Ã°£´ç
100ȸ±îÁöÀÌ´Ù.
³Ã°¡¾Ð½Ç½Ä die casting machine¿¡¼´Â aluminum, Ȳµ¿, ûµ¿ µîÀÇ Çձݰú °°ÀÌ ºñ±³Àû ¿ëÀ¶¿Âµµ°¡ ³ôÀº
±Ý¼ÓÀ» ¿Âµµ°¡ ±×¸® ³ôÁö ¾Ê°í À¯µ¿¼ºÀÌ ³·Àº »óÅ¿¡¼ 200 ~ 300kg/cm©÷ÀÇ °í¾Ð·ÂÀ¸·Î ¿¹¿µÇÁö ¾ÊÀº ±ÝÇü ³»¿¡ ÁÖÀÔ½Ã۸ç,
°è¼Ó °¡¾ÐÇÏ¿© ´ÜÁ¶È¿°ú±îÁö ±â´ëÇÒ ¼ö ÀÖ´Ù.
¹°·Ð ¿°¡¾Ð½Ç½Ä¿¡¼ »ç¿ëµÇ´Â ±Ý¼ÓÀ» ³Ã°¡¾Ð½Ç½Ä¿¡¼µµ ÁÖÁ¶ÇÒ ¼ö ÀÖ´Ù.
-
¢Ð
¿°¡¾Ð½Ç½Ä die casting machine
|
¢Ð
³Ã°¡¾Ð½Ç½Ä die casting machine
|
[2-2] ±ÝÇü(ÐÝúþ; die)
¢Ð
die Àç·á´Â ³»¿¼º°ú ¿Ã³¸®ÀÇ ¾ÈÁ¤¼º, ³»ºÎ½Ä¼ºÀÌ Ä¿¾ß Çϰí, die ±¸Á¶´Â ¾Æ·¡ ±×¸²°ú °°ÀÌ 2Æí(ø¸) ÀÌ»óÀ¸·Î
µÇ¾î ºÐ¸®½ÃÄÑ ÁÖ¹°À» »©³¾ ¼ö ÀÖ¾î¾ß ÇÑ´Ù.
-
dieÀÇ ÀÛµ¿ ¿¹
[3] shell molding ¹ý(shell Á¶Çü¹ý, shell molding process)
±Ý¼Ó¸ðÇüÀ» 250~300¡É·Î °¡¿Çϰí, ±× À§¿¡ ¹Ú¸®Á¦ÀÎ ±Ô¼Ò¼öÁö¸¦ ¹Ù¸¥ ÈÄ 140~200mesh Á¤µµÀÇ SiO©ü¿Í
¿°æÈ¼º ÇÕ¼º¼öÁö(thermosetting resin binder)¸¦ ¹èÇÕÇÑ ÁÖÇüÀç¿¡ ¸ðÇüÀ» ¸Å¸ôÇÏ¿© ÁÖÇüÁ¦ÀÛÀ» ÇÏ´Â ¹æ¹ýÀ»
shell molding ¹ýÀ̶ó Çϸç, ¹ß¸íÀÚ°¡ µ¶ÀÏÀÎ J. CroningÀ̶ó ÇÏ¿© Croning ¹ý ¶Ç´Â C-process¶ó°íµµ ÇÑ´Ù.
¾Æ·¡ ±×¸²°ú °°Àº °úÁ¤¿¡¼ ¸ðÇü¿¡ ÁÖÇüÀç°¡ 15~30secµ¿¾È ¿ëÀ¶ÇÏ¿© Á¢ÇÑ ÈÄ dump box¸¦
¹ÝÀüÇÏ¿© ¹ÝÀÀÇÏÁö ¾ÊÀº °ÍÀº ³«ÇϽÃÄÑ ºÐ¸®Çϸç, ÀÌ °úÁ¤À» settingÀ̶ó ÇÑ´Ù.
¼ºÇüµÈ shellÀ» ¸ðÇü°ú ÇÔ²² 300~350¡É±îÁö 1min µ¿¾È °¡¿·Î¿¡¼ °¡¿½Ã۸ç, ÀÌ °úÁ¤À» curingÀ̶ó ÇÑ´Ù.
curing ÈÄ 5~10mm µÎ²²ÀÇ shellÀ» ¸ðÇü¿¡¼ ºÐ¸®½ÃÄÑ shell½ÖÀ» Á¶¸³ÇÏ¿© ÁÖÇüÀ» Á¦ÀÛÇÑ´Ù.
ÁÖ¹°ÀÌ ÀÛÀ» ¶§¿¡´Â spring ¶Ç´Â clamp µîÀ¸·Î shell¸¦ Á¶¸³Çϰí, Å« ÁÖ¹°¿¡ ´ëÇÏ¿©´Â
¿ëÅÁÀÇ ¾Ð·Â¿¡ ´ëÇÏ¿© shellÀÇ Á¶¸³»óŸ¦ À¯ÁöÇÒ ¼ö ÀÖµµ·Ï ÁÖÇü»óÀÚ¿¡ ¸ð·¡ ¶Ç´Â öÆí µîÀ»
ÀåÀÔÇÑ´Ù.
shellÀÇ °µµ´Â ¼öÁö(â§ò·)ÀÇ Ã·°¡·®, ±ÝÇüÀÇ °¡¿Á¶°Ç, setting ½Ã°£ ¹× curling ½Ã°£ µî¿¡ ÀÇÇÑ´Ù.
-
shell Á¶Çü¹ýÀÇ °øÁ¤ ¹× shell Á¶Çü±â
¢Ð
shell molding ¹ýÀÇ Æ¯Â¡À» µé¸é
-
ÀåÁ¡
- ¹Ì¼÷·Ã°øµµ shell¸¦ Á¦ÀÛÇÒ ¼ö ÀÖ´Ù.
- shellÀ» ÁغñÇÑ ÈÄ ÀϽÿ¡ ÁÖÀÔÇÏ¿© ÁÖ¹°À» ´Ù·®»ý»êÇÒ ¼ö ÀÖ´Ù.
- ö ¹× ºñö ¸ðµç ±Ý¼ÓÀÇ ÁÖÁ¶¿¡ ÀÌ¿ëÇÒ ¼ö ÀÖ´Ù.
- ÁÖ¹°ÀÇ Á¤¹Ðµµ°¡ ³ô´Ù.
-
´ÜÁ¡
- ±ÝÇüÀ» ÇÊ¿ä·Î Çϱ⠶§¹®¿¡ ¼Ò·®ÀÇ ÁÖÁ¶¿¡¼´Â ºñ°æÁ¦ÀûÀÌ´Ù.
- ¼öÁö(â§ò·)°¡ ºñ±³Àû °í°¡À̹ǷΠÁÖÁ¶ºñ°¡ ³ô´Ù.
- shell Á¦ÀÛÀÇ energy ºñ¿ëÀÌ ³ô´Ù.
- öÀÇ ÁÖÁ¶¿¡´Â 10kgÁ¤µµ·Î Á¦ÇѵȴÙ.
[4] investment molding ¹ý(investment molding process, lost-wax process,)
¾ò°íÀÚ ÇÏ´Â ÁÖ¹°°ú µ¿ÀÏÇÑ Çü»óÀÇ ¸ðÇüÀ» wax ¶Ç´Â paraffin µîÀ¸·Î ¸¸µé¾î ÁÖÇüÀç¿¡ ¸Å¸ôÇÏ¿© ´ÙÁø ´ÙÀ½ °¡¿ÇÏ¿©
ÁÖÇüÀ» °æÈ½ÃÅ´°ú µ¿½Ã¿¡ ¸ðÇüÀ» ¿ëÃâ(éÂõó)½ÃÄÑ ÁÖÇüÀ» ¿Ï¼ºÇÏ´Â ÁÖÇüÁ¦ÀÛ¹ýÀ» ¸»Çϸç, Àϸí lost wax ¹ýÀ̶ó°íµµ ÇÑ´Ù.
ÀÌ ÁÖÇü¿¡ ÀÇÇÑ ÁÖÁ¶(investment casting)¿¡¼ ÁÖ¹°ÀÇ Ä¡¼ö Á¤µµ¿Í Ç¥¸é Á¤µµ°¡ ÁÁ±â ¶§¹®¿¡ Á¤¹ÐÁÖÁ¶¹ýÀ̶ó°íµµ ÇÑ´Ù.
ÀÌ ¹æ¹ýÀº ¢Ñ Á¤¹ÐÇϰí Çü»óÀÌ º¹ÀâÇÏ¿© ±â°è°¡°øÀÌ ¾î·Á¿î ¼ÒÇüÁÖ¹°(1g ~ 35kg)ÀÇ
ÁÖÁ¶¿¡ Àû¿ëµÈ´Ù.
ÁÖÁ¶°úÁ¤À» ³ª¿ÇÏ¸é ´ÙÀ½°ú °°´Ù.
- wax ¸ðÇü Á¦ÀÛ¿ë ±Ý¼ÓÁÖÇü¿¡ wax¸¦ 30kg/cm©÷,
ÇÕ¼º¼öÁö´Â 80kg/cm©÷ÀÇ ¾Ð·ÂÀ¸·Î ÁÖÀÔÇÏ¿© ¸ðÇüÀ» ¸¸µé°Å³ª, Àý»èÇÏ¿© ¸¸µç´Ù.
º¹ÀâÇÑ Çü»óÀÇ °ÍÀº Á¢Âø Á¶¸³ÇÑ´Ù.
- wax ¸ðÇü¿¡ Al2O3¿Í Á¡°áÁ¦ÀÎ ethyl silicate µîÀ»
È¥ÇÕÇÑ ³»ÈÀç·á¸¦ µµÆ÷Çϸç, ÀÌ ³»ÈÀç·á¸¦ investment¶ó ÇÑ´Ù.
- ¸ðÇüÀ» ½Ç¿Â¿¡¼ °ÇÁ¶ÇÏ¿© °æÈ½ÃŲ´Ù.
- ¸ðÇüÀ» ÁÖÇüÀç¿¡ ¸Å¸ôÇÏ°í ´ÙÁø´Ù.
- ÁÖÇüÀ» °¡¿ÇÏ¿© ¸ðÇüÀ» ¿ëÃâ½ÃŲ´Ù.
- ÁÖÇüÀ» 500~1000¡ÉÁ¤µµ·Î °¡¿ÇÏ¿© ¿ëÅÁÀÇ À¯µ¿¼ºÀ» ÁÁ°ÔÇÑ´Ù.
- ¿ëÅÁÀ» ÁÖÀÔÇÏ¿© ÀÀ°í½ÃŲ´Ù.
- ÁÖÇü¿¡¼ Á¦Ç°À» ²¨³½´Ù.
-
investment casting °úÁ¤
¢Ð
ÀÌ ¹æ¹ý¿¡ ÀÇÇÑ ÁÖÁ¶¹ýÀÇ Àå´ÜÁ¡Àº ´ÙÀ½°ú °°´Ù.
-
ÀåÁ¡
- Á¤¹ÐÇϰí Çü»óÀÌ º¹ÀâÇÏ¿© ±â°è°¡°øÀÌ ¾î·Á¿î Á¦Ç°ÀÇ ÁÖÁ¶¿¡ ÀûÇÕÇÏ´Ù.
- ¸ðÇüÀç·áÀÎ wax¸¦ Àç»ç¿ëÇÒ ¼ö ÀÖ´Ù.
- À¶Á¡ÀÌ ³ôÀº ö±Ý¼ÓÀÇ ÁÖÁ¶°¡ °¡´ÉÇÏ´Ù.
´ÜÁ¡
- ¼ÒÇü¹°ÀÇ ÁÖÁ¶¿¡ ÇÑÇÑ´Ù.
- ÁÖÁ¶´Ü°è°¡ ¸¹±â ¶§¹®¿¡ ÁÖÁ¶ºñ°¡ ³ô´Ù.
-
[5]Áø°øÁÖÁ¶¹ý(òØÍöñÑðãÛö; vacuum casting) ¢Ð
´ë±â Áß¿¡¼ ö°(ôÑ˼)À» ¿ëÇØÇÏ¿© ÁÖÁ¶Çϸé O©ü, H©ü,
N©üµîÀÇ gas°¡ ¿ëÅÁ¿¡ µé¾î°¡¼ O©ü´Â »êȹ°À» Çü¼ºÇϰí, H©ü´Â
¢Ñ ¹éÁ¡(ÛÜïÇ; white spot, flake) ¶Ç´Â hair crackÀÇ
¿øÀÎÀÌ µÇ¸ç, N©ü´Â °æµµ°¡ Å« ÁúÈöÀ» Çü¼ºÇÑ´Ù. ÀÌ·¯ÇÑ ºÎÀÛ¿ëÀ» ¾ø¾Ö°Å³ª, °¨¼Ò½Ã۱â À§ÇØ
10-3mmHg Á¤µµÀÇ Áø°ø¿¡¼ ÁÖÁ¶ÇÑ´Ù.
ÀÛ¾÷¹æ½Ä¿¡´Â
- ´ë±â¿¡¼ ¿ëÇØ
- Áø°ø¿¡¼ Å» gas ¡æ ´ë±â¿¡¼ ÁÖÀÔ
- Áø°ø¿¡¼ ÁÖÀÔ
- Áø°ø¿¡¼ ¿ëÇØ ¡æ ´ë±â¿¡¼ ÁÖÀÔ
- Áø°ø¿¡¼ ¿ëÇØ ¡æ Áø°ø¿¡¼ ÁÖÀÔ
Áø°ø tank ³»¿¡ ÁÖÇüÀ» ³Ö°í ¿ëÅÁÀ» ÁÖÀÔÇÏ´Â µ¥¿¡ ¾î·Á¿òÀÌ ÀÖÀ¸¸ç, ƯÈ÷ ´ëÇüÀÇ °æ¿ì¿¡´Â ¸¹Àº Á¦¾àÀÌ ÀÖ¾î º¸Åë
¼ÒÇüÀº Áø°ø½Ç ¿ëÇØ ¡æ Áø°ø½Ç ÁÖÀÔÀÌ °¡´ÉÇϳª, ´ëÇüÀº ´ë±â¿¡¼ ¿ëÇØ ¡æ Áø°øÃ³¸® ¡æ ´ë±â¿¡¼ ÁÖÀÔ
¶Ç´Â ºÒȰ¼º gas ºÐÀ§±â¿¡¼ ÁÖÀÔÇÑ´Ù.
(1) Å»(÷) gas ÈÄ¿¡ ÁÖÀÔÇÏ´Â ¹æ¹ý:
¾Æ·¡ ±×¸²°ú °°ÀÌ ´ë±â¿¡¼ ¿ëÇØÇÑ ¿ëÅÁÀÌ ´ã±ä ladle ¶Ç´Â µµ°¡´Ï¸¦ Áø°ø½Ç¿¡ ³Ö¾î ¿ëÅÁÀÇ gas(¼ö¼Ò, »ê¼Ò, Áú¼Ò)¸¦
»©³½ ÈÄ ÁÖÇü¿¡ ÁÖÀÔÇÑ´Ù. ladle ¶Ç´Â µµ°¡´Ï¸¦ Àå½Ã°£ Áø°ø½Ç¿¡ ³õÀ¸¸é ¿Âµµ°¡ °ÇÏÇÑ´Ù´Â °ÍÀ» °í·ÁÇϰí
¿ëÅÁÀÌ boiling ÇÏ¿© ³ÑÄ¡Áö ¾Êµµ·Ï ¿©À¯±íÀ̸¦ µÎ¾î¾ß ÇÑ´Ù.
Å» gas ÀåÄ¡
(2) ÁÖÀԽà Ż gasÇÏ´Â ¹æ¹ý:
¾Æ·¡ ±×¸²°ú °°ÀÌ ladle ¸¶°³¸¦ »Ì°í Áø°ø½Ç ³»¿¡ ÀÖ´Â ÁÖÇü¿¡ ºÎ¾îÁö´Â Áß¿¡ Å» gasÇÏ´Â ¹æ¹ýÀÌ´Ù.
ÁÖÀԽà Ż gasÇÏ´Â ¹æ¹ý
(3) Áø°ø½Ç¿¡¼ ¿ëÇØ ¹× ÁÖÀÔÇÏ´Â ¹æ¹ý:
Áø°ø½Ç ³»¿¡ °íÁÖÆÄÀ¯µµÀü±â·Î, Àü±âÀúÇ×·Î ¶Ç´Â Àü±âÀüÈ£·Î¿Í ÁÖÇüÀ» ³Ö°í ±× ¾È¿¡¼ ¿ëÇØ ¹× ÁÖÀÔÀÛ¾÷ÀÌ
ÀÌ·ç¾îÁöµµ·Ï µÈ ÁÖÁ¶¹ýÀ¸·Î¼ 1000kgÀÌÇÏÀÇ ¼ÒÇü¹°ÀÇ ÁÖÁ¶¿¡ ¸¹ÀÌ Àû¿ëµÈ´Ù.
°¢ ·ÎÀÇ Àå´ÜÁ¡Àº ¿ëÇØ ±Ý¼Ó, ÇÕ±ÝÀÇ Á¾·ù ¹× ¼ººÐÁ¶Á¤ÀÇ Á¤µµ¿¡ µû¶ó ´Ù¸£´Ù.
Áø°øµµ´Â 10-3mmHg~10-4mmHg Á¤µµÀ̸ç,
¿ëÇØ½Ã°£Àº ¾à 2½Ã°£ÀÌ´Ù.
À̹æ¹ý¿¡¼´Â ÁÖÁ¶ÀÇ Àü°úÁ¤¿¡¼ ºÐÀ§±âÀÇ ¿À¿°À» ¹æÁöÇÒ ¼ö ÀÖ´Ù.
[6] Àú¾ÐÁÖÁ¶¹ý(î¸äâñÑðãÛö; low pressure casting, pressure pouring casting, pressure casting)
º¸Åë »çÇüÀ» ÀÌ¿ëÇÏ´Â ÁÖÁ¶¿¡¼´Â ¿ëÅÁÀÇ ÁÖÀÔÀÌ Á߷¿¡ ÀÇÇÏ¿© ÀÌ·ç¾îÁö°í, ¿ø½ÉÁÖÁ¶¹ý ¶Ç´Â die casting¿¡¼´Â ¿ëÅÁ¿¡
¾Ð·ÂÀ» °¡Çϳª, Àú¾ÐÁÖÁ¶¹ý¿¡¼´Â Èæ¿¬ÁÖÇü ¶Ç´Â ±ÝÇü¿¡¼ pump·Î ÈíÀÔÇÏ¿© ÁÖÇü ³»¸¦ Àú¾Ð ¶Ç´Â Áø°øÀ¸·Î Çϰí
±×¸²°ú °°ÀÌ ¿ëÅÁÀ» »¡¾Æ ¿Ã¸®°Å³ª, ºÒȰ¼º gas·Î ¹Ð¾î¿Ã¸°´Ù. ¼öºÐ ÈÄ¿¡ ÁÖÇü ³»ÀÇ ÅÁÀÌ ÀÀ°íµÇ¸é °¡¾ÐÀ» ÁßÁöÇÏ¿©
±ÞÅÁ°ü ³»ÀÇ ÅÁÀ» ³«ÇϽÃŲ´Ù.
ÀÌ ÁÖÁ¶¹ý¿¡ ÀÇÇÏ¸é ¹Ðµµ¿Í °µµ°¡ Å©¸ç, ¿ëÅÁ¼ÓÀÇ ±Ý¼ÓÀÌ °ø±ÞµÇ±â ¶§¹®¿¡ ºÒ¼ø¹°ÀÌ ÀûÀº
¢Ñ °í±ÞÁÖ¹°ÀÌ ¾ò¾îÁø´Ù.
ƯÈ÷ aluminum°ú °°ÀÌ ´ë±â Áß¿¡¼ »êȰ¡ ½ÉÇÑ ±Ý¼ÓÀÇ ÁÖÁ¶¿¡ À¯¸®ÇÏ´Ù.
-
Àú¾ÐÁÖÁ¶¹ý
¢Ð
[7] ¿¬¼ÓÁÖÁ¶¹ý(ææáÙñÑðãÛö; continuous casting)
ºÀÀç, ÆÇÀç ¹× ±¸Á¶¿ëÀç´Â ÀϹÝÀûÀ¸·Î ¿ëÇØ ¡æ Á¶±«(ðãÎÔ) ¡æ °¡¿ ¡æ ºÐ±«(ÝÂÎÔ) ¡æ °¡¿ ¡æ
¢Ñ ¾Ð¿¬
µîÀÇ °úÁ¤À» °ÅÃÄ ¸¸µé¾îÁö³ª ±×¸²°ú °°ÀÌ ¿ëÀ¶±Ý¼Ó¿¡¼ Á÷Á¢ ¾Ð¿¬¿¡ µé¾î°¡´Â billetÀ»
ÁÖÁ¶ÇÔÀ¸·Î½á À§ÀÇ °øÁ¤ Áß¿¡¼ Á¶±«(ðãÎÔ) ¡æ °¡¿ ¡æ ºÐ±«(ÝÂÎÔ) ¡æ °¡¿ÀÇ °øÁ¤À»
»ý·«ÇÒ ¼ö ÀÖ´Ù. ÀÌ ¶§ Á¦Ç°ÀÇ ±Ô°Ý¿¡ µû¶ó ÁÖ±«(ñÑÎÔ; ingot)ÀÇ ´Ü¸éÄ¡¼ö¿Í ±æÀ̰¡ Á¤ÇÏ¿© Áø´Ù.
ingotÀº º¸Åë ingot case¿¡ ÁÖÀÔÇÏ¿© ¸¸µå³ª caseÀÇ ¼ö¸íÀÌ Âª°í ingotÀÌ ºÒ±ÕÀÏÇÏ°Ô µÇ¹Ç·Î
¿¬¼ÓÁÖÁ¶¹ýÀ» ÀÌ¿ëÇϸé
- Æí¼®(ø¶à°)ÀÌ Àû°í,
- ³Ã°¢Á¶°Ç¿¡ µû¶ó Á¶Á÷À» Á¶Á¤ÇÒ ¼ö ÀÖÀ¸¸ç,
- ¼öÃà°ø(â¥õêÍî)ÀÌ ¾ø°í,
- ÁÖ¹°Ç¥¸éÀÌ ¸Å²ô·´°í,
- ´Ü¸éÄ¡¼ö¸¦ Á¶Á¤ÇÒ ¼ö ÀÖ°í,
- ¾Ð¿¬½Ã¿¡ Àç°¡¿ÇÒ Çʿ䰡 ¾ø´Â µîÀÇ
ÀåÁ¡ÀÌ ÀÖ´Ù.
±×·¯³ª ½Ã¼³ÀÌ °í°¡À̹ǷΠ¼Ò·® ´Ùǰ»ý»ê¿¡´Â ºÎÀûÇÕÇÏ´Ù.
-
¿¬¼ÓÁÖÁ¶¹ý ¢Ð
|
¿¬¼ÓÁÖÁ¶°úÁ¤À» º¸¿©ÁØ´Ù.
|
[8] CO©ügas Á¶Çü¹ý(carbon-dioxide molding process)
´Ü½Ã°£¿¡ °ÇÁ¶ÇüÀ» ¾ò´Â °Í°ú °°Àº È¿°ú¸¦ º¸´Â Á¶Çü¹ýÀ¸·Î¼, ÁÖÇüÀçÀÎ ÁÖÇü»ç¿¡ ¹°À¯¸®(±Ô»ê¼Ò´Ù)¸¦ 1.5~6%
Á¤µµ ÷°¡ÇÏ¿© ¸¸µç ÁÖÇü¿¡ CO©ügas¸¦ ħÅõ½ÃÄÑ °æÈÇÑ´Ù.
CO©ügas¸¦ 1 ~ 1.5±â¾ÐÀ¸·Î 5sec µ¿¾È ħÅõ½Ã۰í ÁÖÇü»ç 0.5kgÀÇ Áõ°¡¸¶´Ù
½Ã°£À» 1secÀÇ ºñÀ²·Î Áõ°¡½ÃŲ´Ù. CO©ügas ºÐ»ç½Ã µ¿°á(ÔÐÌ¿)À» ¹æÁöÇϱâ
À§ÇÏ¿© CO©ügas bomb¿¡ °¡¿ ÀåÄ¡¸¦ µÐ´Ù. CO©ügas ÁÖÇüÁ¦ÀÛ¹ýÀº Å« °µµÀÇ
core°¡ ÇÊ¿äÇÒ ¶§µµ ÀÌ¿ëµÈ´Ù.
-
CO©ügas Á¶Çü¹ý
¢Ð
CO©ügas Á¶Çü¹ýÀÇ Æ¯Â¡À» µé¸é
-
ÀåÁ¡
- ¹èÇÕºñÀ²·Î ÁÖÇüÀÇ °µµ¸¦ Á¶Á¤ ÇÒ ¼ö ÀÖ´Ù.
- Á¶ÇüÀÌ ¿ëÀÌÇÏ´Ù.
- ´Ü½Ã°£¿¡ °ÇÁ¶ÇüÀÇ È¿°ú¸¦ ¾òÀ» ¼ö ÀÖ´Ù.
- ¼÷·ÃÀÚ°¡ ÇÊ¿ä ¾ø´Ù.
- gas ¹ß»ýÀÌ Àû°í, °ÇÁ¶¿¡ ÀÇÇÑ º¯ÇüÀÌ ¾ø¾î ÁÖ¹°ÀÇ Ä¡¼ö Á¤¹Ðµµ°¡ ³ô´Ù.
-
´ÜÁ¡
- Á¶Çü ÈÄ ÁÖÀԽñîÁö ³Ê¹« Àå½Ã°£ ¹æÄ¡ÇÏ¸é ´ë±â¿¡¼ ¼öºÐÀ» Èí¼öÇÏ¿© ÁÖÇüÀÇ °µµ°¡ ¶³¾îÁø´Ù.
- ÁÖÀÔ ÈÄ ÁÖ¹°À» ²¨³¾ ¶§ ÁÖÇüÀÇ ÇØÃ¼°¡ Èûµç´Ù.
- ÁÖÇü»çÀÇ º¹¿ë¼ºÀÌ ¾ø´Ù.