Die Casting
The traditional diecasting process is the injection under high pressure into a steel mould (otherwise known
as a tool or die) of a molten metal alloy. This solidifies rapidly (in a few seconds) to form a net-shaped component,
which is then automatically extracted.
The majority of zinc components, and non-ferrous components in general, are produced by the high-pressure
diecasting process.
There are two basic diecasting processes, differentiated only by their methods of metal injection:
hot-chamber and cold-chamber. The hot-chamber process is only used for the zinc alloys(except ZA-27)
and magnesium alloy AZ-91. Aluminium can only use the cold-chamber process due to aluminium alloys eroding the
immersed steel of the hot-chamber injection mechanism.
The metal injection portion of the cycle normally terminates with a sharp intensification of metal pressure.
This is developed by increasing the hydraulic pressure on the plunger, forcing additional metal
into the die cavity to supplement the shrinkage that takes place during solidification.
It is beneficial to the extent that it promotes complete filling of the die cavity and creates
a uniform metal density. Excessive intensification is undesirable, because it forces molten metal
between die members, causing die wear and excessive flash which must subsequently be removed.
The peak pressure multiplied by the projected area of the entire shot generates the force
imposed on the machine structure. This pressure often dictates the size of the machine required
to make a casting, which in turn affects the cost of the finished product. Machines are rated by
the number of tonnes locking force capable of being developed in long-term, continuous operation.
The casting is normally ejected from the die, attached to extra material. This includes the gate,
runner, any overflows and possibly flash. Collectively, all of this material
(known as the shot) is then transferred to a trim die, which separates the casting from the extraneous material.
This trimmed metal is subsequently recycled.
|
The hot-chamber process is only used for zinc and other low melting point alloys that do not
readily attack and erode metal pots, cylinders and plungers. Development of this technology,
through the use of advanced materials, allows this process to be used for some magnesium alloys.
The basic components of a hot-chamber diecasting machine and die are illustrated below.
In this process, the plunger and cylinder, which constitute the injection mechanism,
are submerged in the molten metal in the crucible (or pot), which is integral to the machine.
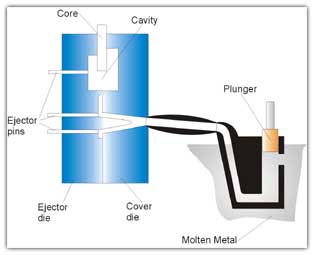
1. The die is closed and the piston rises, opening the port and allowing molten metal to fill the cylinder.
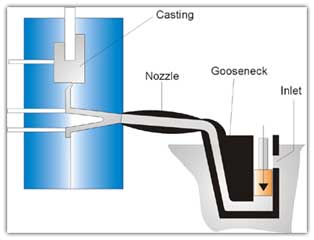
2. The plunger moves down and seals the port pushing the molten metal through the gooseneck and nozzle
into the die cavity, where it is held under pressure until it solidifies.
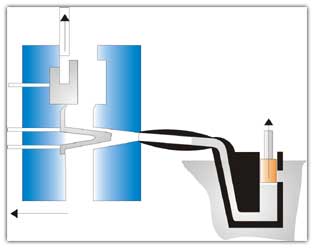
3. The die opens and the cores, if any, retract. The casting remains in only one die, the ejector side.
The plunger returns, allowing residual molten metal to flow back through the nozzle and gooseneck.
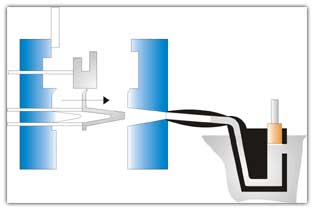
4. Ejector pins push the casting out of the ejector die. As the plunger uncovers the filling hole,
molten metal flows through the inlet to refill the gooseneck, as in step (1).
|
The cold-chamber diecasting differs from hot-chamber in that the injection system is not submerged in molten metal.
Instead, the molten charge (more material than is required to fill the casting) is ladled from the crucible
into a shot sleeve, where a hydraulically operated plunger pushes the metal into the die. The extra material
is used to force additional metal into the die cavity to supplement the shrinkage that takes place during
solidification. The principle components of a cold-chamber diecasting machine are shown below.
Injection pressures over 10,000 psi or 70,000 KPa can be obtained from this type of machine.
1. The die is closed and the molten metal is ladled into the cold-chamber shot sleeve.
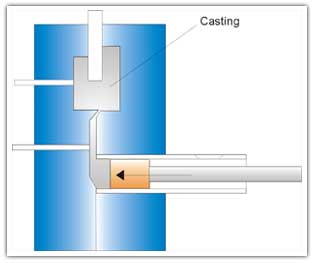
2. The plunger pushes the molten metal into the die cavity where it is held under pressure until solidification.
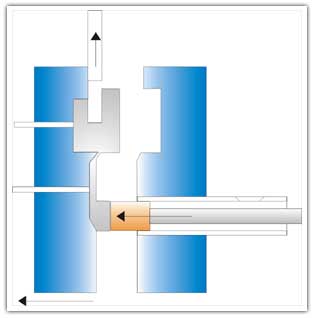
3. The die opens and the plunger advances, to ensure that the casting remains in the ejector die. Cores, if any, retract.
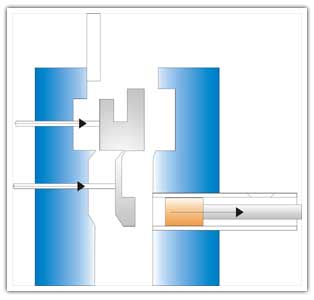
4. Ejector pins push the casting out of the ejector die and the plunger returns to its original position.
|
Advantages of Hot-Chamber Over Cold-Chamber
- Rapid cycling, starting from less than 1 second for miniature zinc components.
- Precise control of metal temperature, improving fluidity, and allowing injection pressures to be lower,
which places less strain on equipment. Better fluidity promotes good filling of the cavity, sounder castings
and permits thinner walls.
- The submerged shot cylinder (gooseneck), which fills automatically, eliminates a variable, reduces the cycle time,
and makes it easier to control metal temperature.
- There is no cooling of the charge (measured shot), as there may be when molten metal is transferred to the shot
cylinder of the cold-chamber machine.
- The molten metal is less subject to oxidation and contaminants from atmospheric exposure.
Disadvantages of Hot-Chamber Process
- Alloy limitations, as aluminium or zinc-aluminium alloys and certain magnesium alloys can only be cold-chamber
processed.
- Lower injection pressures and speed can be achieved, so castings may be less dense.
- Higher maintenance costs.
|
Advantages of Cold-Chamber Over Hot-Chamber
- Alloys such as aluminium or zinc-aluminium alloys and certain magnesium alloys can only be cold-chamber processed.
- Higher injection pressures and speed can be achieved, producing denser castings.
- Lower maintenance costs.
Disadvantages of Cold-Chamber Process
- Slower cycling.
- Less control of metal temperature, reduced fluidity and thin wall capability.
- The charge (measured shot) cools prior to injection.
- The molten metal is subject to oxidation and contaminants from atmospheric exposure.
|