¿Ç³¿ëÁ¢(hot gas welding)
Process background
Hot gas welding is a fabrication process for thermoplastic materials. The process, invented in
the mid 20 th century, uses a stream of heated gas, usually air, to heat and melt both the thermoplastic
substrate material and the thermoplastic welding rod. The substrate and the rod fuse to produce a weld.
Welding materials
There are two groups of plastic materials; thermoplastics and thermosets. The hot gas welding technique
is only applicable to those plastic materials that can be heated and melted repeatedly, namely
thermoplastics.
When a thermoplastic is heated, the molecular chains become mobile within the material and allow it
to melt and flow.
Thermosets are a group of plastic materials in which the molecular chains form cross-links. These
cross-links, formed by a chemical reaction, prevent the molecular chains becoming mobile when heat
is applied.
Although many thermoplastics can be welded by this process, the most common are polypropylene, polyethylene,
PVC and some fluoropolymers such as PVDF, FEP and PFA.
Extruded rod and sheet are the most commonly used raw materials for the manufacture of fabricated plastic
products. It is of utmost importance when fabricating plastics that the welding rod and the sheet are of
identical material and chemical type.
For example, although it is possible to weld polypropylene homopolymer to polypropylene random block
copolymer, the strength of the weld will be reduced significantly. It is also important to check the
quality of the welding rod prior to use, since air bubbles within the rod can form during the extrusion
process. These will lead to voids in the weld. Welding rods will typically be either three or four
millimetres in diameter.
Welding parameters
There are four main welding parameters in the hot gas welding process: temperature, pressure,
welding speed and gun position. Since the process is manual, it is important that the welder has a good
understanding of the need to ensure that all four of these parameters are correct and controlled during
the welding operation.
Temperature is the most important of the four parameters, since the temperature at the interface between
the rod and the substrate is not only controlled by the setting on the gun, but also by the gun travel
speed and the gun position with respect to the substrate.
Typically, the temperature for welding is set between 80 and 100¡ÆC above the melting point of the material
being welded. The gun travel speed is normally between 0.1 and 0.3m/min, again, depending upon the material
being welded.
The welding pressure is applied via the toe of the welding nozzle and is achieved by holding the welding
gun grip firmly and pushing down into the weld. For round nozzle welding, pressure is applied manually
from the welding rod.
The correct welding pressure is easier to achieve using welding guns with the fan separate to the gun
since a firmer grip around the handle can be achieved. The force applied to the welding rod would
typically be between 15 and 30N.
Weld quality
As a manual process, weld quality is dependent on skill. There is no recognised non-destructive technique,
that conclusively shows the presence of defects in plastic welds that could lead to weld failure. Therefore,
it is recommended that good quality welder training is received and that welder certification is adopted.
The European Standard (EN13067) sets out the criteria for plastic welder approval. It details a scheme
where the welder undergoes both a theoretical and a practical test and the welder, upon successful completion,
is awarded a certificate of approval in the specific material categories taken in the test. Certification
lasts for two years with a further two years prolongation, effectively giving the welder an approval
certificate for four years before requiring a full retest.
There are three welding techniques:
|
(2) speed welding
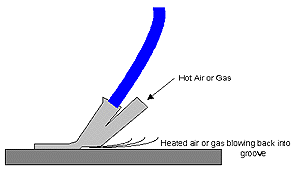
¿ëÁ¢ºÀÀ» hot gas nozzle¿¡ ºÎÂøµÈ tube¸¦ ÅëÇÏ¿© °ø±Þ ÇÏ°í ¸ðÀç¿Í ¿ëÁ¢ºÀÀ» µ¿½Ã¿¡
°¡¿ÇÏ¸é¼ bead¿¡ ¾Ð·ÂÀ» °¡ÇÑ´Ù.
This is the plastic welding technique equivalent to gas welding. However, the techniques are only
vaguely similar. A specially designed heat gun (hot air welder) produces a jet of hot air that softens
the parts to be joined, as well as the plastic weld rod. Hot gas welding is a common fabrication technique
for manufacturing smaller items including and not limited to chemical tanks, heat exchangers, and plumbing
fittings. The materials being welded and the welding rod must be of the same or very similar plastic.
Welding PVC to acrylic is an exception to this rule.
|
(3) extrusion welding
¹Ý¿ëÀ¶ ¶Ç´Â ¿ÏÀü ¿ëÀ¶ »óÅÂÀÇ polymer¸¦ ä¿ö¼ ¿ëÁ¢ ÇÑ´Ù.
Extrusion welding allows the application of bigger welds in a single weld pass. It is the preferred
technique for joining material over 6 mm thick. Welding rod is drawn into a miniature hand held plastic
extruder, plasticized, and forced out of the extruder against the parts being joined, which are softened
with a jet of hot air to allow bonding to take place.
|