[5] ¾ÐÃà°¡°ø(äâõêÊ¥Íï)(±³°ú¼ p.274)
º» ¾ÐÃà°¡°ø¿¡¼´Â »ó¡¤ÇÏÀÇ die »çÀÌ¿¡ ÆÇÀ縦 ³Ö°í ¾ÐÃà·ÂÀ» °¡ÇÏ¿© ÆÇ¿¡ ¿äö(èêôÈ)À» ³»´Â ¾ÐÀΰ¡°ø(coining)°ú
ºÎÁ¶°¡°ø(embossing)¸¸À» Ãë±ÞÇÑ´Ù.
±×¸²°ú °°ÀÌ ¼ÒÀ縦 »ó¡¤ÇÏ¸é »çÀÌ¿¡¼ ¾ÐÃàÇÒ ¶§ ¾ÐÃà¸éÀûÀ» A ,
´ÜÀ§¸éÀûÀÇ ¾ÐÃàÀúÇ×À» kf¶ó ÇÏ¸é ¾ÐÃà·Â P´Â ´ÙÀ½°ú °°´Ù.
|
¾ÐÃà°¡°ø
|
[5-1] ¾ÐÃà°¡°ø¹æ½Ä
(1) ¾ÐÀΰ¡°ø(äâìÔÊ¥Íï; coining):
±×¸²°ú °°ÀÌ ¼ÒÀç¸é¿¡ ¿äö(èêôÈ)À» ³»´Â °¡°øÀ¸·Î¼, °¡°ø¸éÀÇ Çü»óÀº À̸é(ìÀØü)ÀÇ °Í°ú´Â ¹«°üÇϸç
ÆÇµÎ²²ÀÇ º¯È¿¡ ÀÇÇÑ °¡°øÀÌ´Ù. ÈÆó(ü§øÇ), medal, badge, ¹®ÀÚ µîÀ» ¾ÐÀΰ¡°øÇÏ´Â °æ¿ì°¡ ¸¹À¸¸ç,
Çü´ÜÁ¶(úþÓ´ðã; colsed-die forging)ÀÇ ÀÏÁ¾À¸·Î¼ À±È°Çϸé À±È°À¯°¡ °ø°£À» Â÷ÁöÇÏ¿© ¼ºÇüÀÌ Á¦´ë·Î µÇÁö ¾Ê´Â´Ù.
¾ÐÀΰ¡°øÀÇ punch ·Â Pc´Â
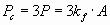
Á¤µµ ÀÌ´Ù.
|
¾ÐÀΰ¡°ø
|
-
(2) ºÎÁ¶°¡°ø(Ý©ðÁÊ¥Íï; embossing):
±×¸²°ú °°ÀÌ ¿äöÀÌ ÀÖ´Â die¿Í punch·Î ÆÇÀ縦 ´·¯ ÆÇ¿¡ ¿äöÀ» ³»´Â °¡°øÀ¸·Î¼, ÀÏÁ¾ÀÇ shallow drawingÀ̸ç
ÆÇÀÇ À̸é(ìÀØü)¿¡´Â Ç¥¸é°ú ¹Ý´ëÀÇ ¿äöÀÌ »ý±â¾î ÆÇÀÇ µÎ²²¿¡´Â º¯È°¡ °ÅÀÇ ¾ø´Ù. ÀÌ °¡°ø¹ýÀº Àå½ÄǰÀÇ °¡°ø ¶Ç´Â
ÆÇÀÇ °¼ºÀ» ³ôÀÌ´Â µ¥ »ç¿ëµÈ´Ù. µû¶ó¼ ºÐ·ù»ó ±ÁÈû°¡°øÀ̳ª drawing¿¡ ¼ÓÇÒ ¼ö ÀÖÀ¸³ª coining°ú ´ëÁ¶°¡ µÇ¾î
¿©±â¿¡¼ ¼Ò°³ÇÑ´Ù.
ºÎÁ¶°¡°ø
|
ºÎÁ¶°¡°ø
|
[6] ¹ÚÆÇƯ¼ö¼ºÇü°¡°ø(ÚÝ÷ù÷åâ¨à÷û¡Ê¥Íï)
(1) °í¹«¾Ð¿¡ ÀÇÇÑ ¼ºÇü(rubber forming):
¾Õ¿¡¼´Â die°¡ °¼ºÀÌ Å« °íü·Î µÇ¾î ÀÖÀ¸³ª, °í¹«¾Ð·Â¿¡ ÀÇÇÑ ¼ºÇü¿¡¼´Â ¾î´À ÇÑÂÊÀÌ °í¹«·Î µÇ¾î
Àֱ⠶§¹®¿¡ °í¹«¿¡ Á¢ÇÏ´Â ÃøÀÇ ¼ºÇüÁ¦Ç°¿¡ scratch ¶Ç´Â ±âŸ ¼Õ»óÀÌ ¾øÀ¸¸ç, º¹ÀâÇÑ Çü»óÀÇ ¼ºÇüµµ
°¡´ÉÇÏ´Â µî »ç¿ë¹üÀ§ÀÇ À¶Å뼺ÀÌ Å©´Ù.
Marform ¹æ¹ýÀº
Marform¿¡ ÀÇÇÏ¿© °³¹ßµÈ °ÍÀ¸·Î¼, ±×¸²°ú °°ÀÌ punch¸¦ ¾Æ·¡ÂÊ¿¡ , °í¹« µîÀÇ Èí¾ÐÀç(ýåäâî§)·Î µÈ die°¡
À§ÂÊ¿¡ ³õ¿© ÀÖ´Ù. À̹æ¹ýÀÇ Æ¯Â¡Àº flange°¡ ÀÛ¾ÆÁ® ¼ÒÀç°¡ ÆÄ¿µÉ °¡´É¼ºÀÌ Àû¾îÁö¹Ç·Î ¸ð¼¸®ÀÇ ¹ÝÁö¸§À»
ÀÛ°Ô ÇÒ ¼ö ÀÖ´Ù´Â °Í°ú °¡°øÁß punchÀÇ Ãø¸é¿¡ ¼öÆò¾Ð·ÂÀÌ ÀÛ¿ëÇÏ´Â °Í µîÀÌ´Ù.
Marform ¼ºÇü°øÁ¤
|
drawing ±íÀÌ¿Í °í¹«ÀÇ ¾Ð·Â
|
-
Guerin ¹æ¹ýÀº
¾Æ·¡ ±×¸²°ú °°ÀÌ die À§¿¡ blank¸¦ ³õ°í °í¹« die·Î °¡¾ÐÇÏ¿© ¼ºÇüÇÏ´Â ¹æ¹ýÀ̸ç, °í¹«°¡ ¹ØÀ¸·Î ¹Ð·Á³ª¿ÀÁö
¾Êµµ·Ï retainer°¡ ¼³Ä¡µÇ¾î ÀÖ´Ù. Ư¡Àº die °ªÀÌ ½Î´Ù´Â °Í°ú die¸¦ °íÁ¤ÇÒ ÇÊ¿ä ¾øÀÌ ³õ±â¸¸ ÇÏ¸é µÈ´Ù´Â
°Í µîÀÌ´Ù. Marform ¹æ¹ý°ú ´Ù¸¥ Á¡Àº ¾ÐÆÇÀÌ ¾ø°í ¾èÀº drawing¿¡ ÀÌ¿ëµÈ´Ù´Â °ÍÀÌ´Ù.
Guerin ¼ºÇü°øÁ¤
(2) ¾×¾Ð¼ºÇü¹ý(äûäâà÷û¡Ûö: hydroforming):
Cincinnati Milling and Grinding Machine Inc.¿¡¼ °³¹ßÇÑ ¼ºÇü¹ýÀ¸·Î¼, Marform ¹æ¹ý¿¡¼ °í¹« ´ë½Å¿¡
¾×ü¸¦ »ç¿ëÇÑ °ÍÀÌ´Ù. ±×¸²°ú °°ÀÌ 2°³ÀÇ °í¹«¸· Áß Çϳª´Â ¾×ü¹ÐÆó¿ëÀ̰í, ´Ù¸¥ Çϳª´Â blank¿Í Á¢ÃËÇÏ´Â
¼ºÇü¿ëÀÌ´Ù. punch°¡ »ó½ÂÇÏ¿© ¾×¾ÐÀ» Á¶ÀýÇϸç, 1000kg/cm©÷±îÁö ¾Ð·ÂÀ»
¾òÀ» ¼ö ÀÖ´Ù. ¶Ç´Â punchÀÇ ¿îµ¿¿¡ ÀÇÇÏÁö ¾Ê°í ¾×¾Ð½ÇÀÇ ¾Ð·ÂÀ» µ¶ÀÚÀûÀ¸·Î 600kg/cm©÷±îÁö
¿Ã¸± ¼ö ÀÖ´Ù. ÀÌ ¹æ¹ýÀÇ Æ¯Â¡Àº ÀÛ¾÷ Áß ¾Ð·ÂÀ» ÀÚÀ¯·ÎÀÌ Á¶ÀýÇÒ ¼ö ÀÖ´Ù´Â °ÍÀÌ´Ù.
¾×¾Ð¼ºÇü°øÁ¤ ¢Ð
(3) bulging:
±×¸²°ú °°ÀÌ ÃÖ¼Ò Áö¸§À¸·Î ¼ºÇüµÈ ¿ë±â¿¡ °í¹«¸¦ ³Ö°í ¾ÐÃàÇÏ´Â °í¹« bulging°ú ¾×ü¸¦ ³Ö´Â ¾×ü bulgingÀÌ ÀÖ´Ù.
°í¹« bulgingÀº ±×¸²°ú °°ÀÌ °í¹«¸¦ ³Ö°í ¾ÐÃàÇÏ¸é °í¹«°¡ °¡·Î ¹æÇâÀ¸·Î ÆØÃ¢ÇÏ¸é¼ ¿ø¿ë±â(ê«é»Ðï)¸¦
die Çü»óÀ¸·Î ¼ºÇüÇÑ´Ù.ÀÌ ¹æ¹ý¿¡¼´Â die¸¦ ÃÖ´ë Áö¸§ºÎ¿¡¼ ºÐ¸®ÇÒ ¼ö ÀÖ°Ô µÇ¾î¾ß Á¦Ç°À» »©³¾ ¼ö ÀÖ´Ù.
À̹æ¹ýÀ¸·Î ¿ë±â»Ó ¾Æ´Ï¶ó ¶Ñ²±¿¡ ³ª»ç¸¦ ¼ºÇüÇÒ ¼öµµ ÀÖ´Ù.
¾×ü bulging¿¡¼´Â ¾Õ¿¡¼ ¼³¸íÇÑ °í¹« bulging¿¡¼ °í¹« ´ë½Å¿¡ ¾×ü¸¦ °í¹«ÁÖ¸Ó´Ï¿¡ ³Ö¾î »ç¿ëÇÑ´Ù.
ÀÌ ¹æ¹ý¿¡ ÀÇÇÏ¿© deep drawingÀÇ ³°üÀÎ flange ÁÖ¸§»ìÀÌ ÇØ°áµÈ´Ù. ±×¸² (c)´Â µî¹Ý»ç°æÀÌ´Ù.
bulging
(4) beading:
±×¸²°ú °°ÀÌ ¿äöÀÌ ÀÖ´Â ÇѽÖÀÇ die ¶Ç´Â rollerÀ» »ç¿ëÇÏ¿© ÆÇ¿¡ Ȩ°ú µ¹±â¸¦ ¼ºÇüÇÏ´Â °¡°øÀ¸·Î¼, º¸°(ÜÍË)À̳ª
Àå½ÄÀÌ ¸ñÀûÀÌ´Ù.
(5) spinning:
¼±¹ÝÀÇ ÁÖÃà°ú °°Àº ȸÀüÃà¿¡ die¸¦ °íÁ¤ÇÏ°í ±× die¿¡ blank¸¦ ½É¾Ð´ë·Î ´·¯ blank¸¦ die¿Í ÇÔ²² ȸÀü½Ã۸é¼
spinning stickÀ̳ª roll·Î blank¸¦ die¿¡ ¹Ð¾î ºÙÀ̾î die Çü»óÀÇ Á¦Ç°À¸·Î ¼ºÇüÇÏ´Â °¡°ø¹ýÀ¸·Î¼,
µµÀÚ±âÀÇ ¼ºÇü¹ý°ú À¯»çÇÏ´Ù.
die·Î´Â ±Ý¼Ó ¶Ç´Â °æ¸ñÀç(ÌãÙÊî§)¸¦ »ç¿ëÇϸç, blank¿Í stickÀº ¸¶ÂûÀÌ ½ÉÇϹǷΠºñ´© µîÀ¸·Î À±È°ÇÏ´Â °ÍÀÌ ÇÊ¿äÇÏ´Ù.
spinningÀº º¸Åë »ó¿Â¿¡¼ ½ÃÇàÇϳª Àü¼ºÀÌ ³·Àº ±Ý¼Ó ¶Ç´Â µÎ²²°¡ Å« blank¿¡ ´ëÇÏ¿©´Â °¡¿ÇÏ¿© °¡°øÇÑ´Ù.
°ø±¸ÀÎ stick ¶Ç´Â rollÀº ¼öµ¿À̳ª ÀÚµ¿À¸·Î ÀÛµ¿½ÃŲ´Ù. ±×¸² (a)¿Í °°ÀÌ ¾ãÀº blank¸¦ die¿¡ ´·¯ ´ë¾î
blank Á÷°æÀ» °¨¼Ò½ÃÄÑ ¼ºÇüÇÏ´Â spinningÀ» conventional spinning À̶ó Çϰí,
±×¸² (b)¿Í °°ÀÌ ¼ÒÀçÀÇ ÃÖ´ëÁ÷°æÀ» À¯ÁöÇϰí, º®ÀÇ µÎ²²¸¦ ¾ã°ÔÇÏ¸é¼ ¼ºÇüÇÏ´Â spinningÀ» shear spinningÀ̶ó ÇÑ´Ù.
deep drawing¿¡¼´Â ¿øÅë¿ë±â ¹× °¢Åë¿ë±â¸¦ ¸¸µé ¼ö ÀÖÀ¸³ª spinning¿¡¼´Â ´Ü¸éÀÌ ¿øÇüÀÎ °Í ¸¸À» °¡°øÇÑ´Ù.
spinning Á¦Ç° ¿¹ ¢Ð
|
spinning ¢Ð
|
CNC spinning
(6) curling:
¾Æ·¡ ±×¸²°ú °°ÀÌ ÆÇÀç ¶Ç´Â ¿ë±â µîÀÇ °¡ÀåÀÚ¸®¸¦ µÕ±Û°Ô ÇÏ´Â °¡°ø¹ýÀ̸ç, beading°ú °°ÀÌ
º¸°, Àå½Ä ¹× Ãë±Þ¿¡ ¾ÈÀüÀ» ÁÖ´Â °ÍÀÌ ¸ñÀûÀÌ´Ù.
curlingÀÇ ¿ø¸®´Â °£´ÜÇϳª °î·ü¹Ý°æÀÌ À۾Ƽ curlÀÇ ³»¿Ü´Â ¾ÐÃà°ú ÀÎÀåÀ» ½ÉÇϰÔ
¹Þ±â ¶§¹®¿¡ º¸Åë ´ÙÀ½ÀÇ Á¶°Ç ³»¿¡¼ ÀÛ¾÷ÇÏ´Â °ÍÀÌ ¾ÈÀüÇÏ´Ù.
- curlÀÇ ¾ÈÁö¸§Àº ÆÇµÎ²²ÀÇ 3 ~ 8¹è Á¤µµ°¡ Àû´çÇÏ´Ù.
- curling ÇÒ ÅëÀÇ Áö¸§ÀÌ ³Ê¹« ÀÛÀ¸¸é curl ³»¿ÜÀÇ º¯ÇüÂ÷°¡ Å©±â ¶§¹®¿¡ ±Õ¿ÀÌ »ý±â¹Ç·Î ÅëÀÇ Áö¸§Àº ÆÇµÎ²²ÀÇ
30¹è ÀÌ»óÀ̾î¾ß Çϰí, ÆòÆÇÀÇ °æ¿ì¿¡´Â curl Áö¸§ÀÌ ÆÇµÎ²²ÀÇ 2¹è±îÁö °¡´ÉÇÏ´Ù.
ÆòÆÇ¿¡ curling
|
¿øÅë¿¡ curling
|
(7) flange °¡°ø(flanging):
ÆÇÀÇ °¡ÀåÀÚ¸®¸¦ ±ÁÇô¼ flange¸¦ ¸¸µå´Â °¡°øÀ¸·Î¼, ±×¸² (A)¿Í °°ÀÌ ¿ÜÇü¼±ÀÌ ¿À¸ñ²Ã(concave)À»
ÃëÇϰí ÀÖ´Â flange´Â ½ÅÀå(ãßíå)À» ¹ÞÀ¸¹Ç·Î ½ÅÀå flange(stretch flange)¶ó Çϰí, ±×¸² (B)¿Í °°ÀÌ
¿ÜÇü¼±ÀÌ º¼·Ï²Ã(convex)À» ÃëÇϰí ÀÖ´Â flange´Â ¼öÃàÀ» ¹ÞÀ¸¹Ç·Î ¼öÃà flange(shrink flange)¶ó ÇÑ´Ù.
Áï ¿øÅëÀÇ °¡ÀåÀÚ¸®¸¦ ¿ÜÃøÀ¸·Î ±ÁÇô ¸¸µç °ÍÀº ½ÅÀå flangeÀ̰í, ¿øÅëÀÇ °¡ÀåÀÚ¸®¸¦ ³»ÃøÀ¸·Î ±ÁÇô ¸¸µç
°ÍÀ» ¼öÃà flange¶ó ÇÒ ¼ö ÀÖ´Ù.
Al ¶Ç´Â ´Ù¸¥ °æÇÕ±Ý(ÌîùêÐÝ) µîÀº ½Ç¿Â¿¡¼ Marform ¼ºÇü¹ý µîÀ¸·Î flange °¡°øÀ» ÇÒ ¼ö ÀÖÀ¸³ª,
Ç׺¹ÀÀ·Â¿¡ ´ëÇÑ Åº¼º°è¼öÀÇ ºñ°¡ ÀÛÀº Mg ¹× Ti µîÀº springback, Á±¼(ñ¨ÏÝ), ±Õ¿ µîÀ¸·Î
ºÒ·®Ç°ÀÌ µÇ±â ½±´Ù.
flange
(8) ÀÎÀ强Çü¹ý(ìÚíåà÷û¡Ûö; stretch forming):
ÆÇ±ÝÀÇ °¡ÀåÀÚ¸®¸¦ clampingÇÏ¿© ÀÎÀåÇÏ°í ¼ºÇü die ¶Ç´Â ¼ºÇü blockÀ» ¼ºÇü±â¿¡ µû¶ó ¾Ð»ó, Çϰ ¹× Ãø¸éÀ¸·Î
À̼۽ÃÄÑ ¼ÒÀ縦 Ç׺¹ÀÀ·Â ÀÌ»ó±îÁö ÀÎÀåÇÏ´Â °¡°ø¹ýÀ¸·Î¼, Ç×°ø±â, ÁöºØ panel µîÀÇ ¼ºÇü¿¡ ¸¹ÀÌ ÀÌ¿ëµÈ´Ù.
±×¸² (a)¿¡¼´Â ¼ºÇü punch die°¡ ¼öÁ÷À¸·Î À̵¿ÇÒ ¶§ ÀÎÀå jaw°¡ ¼öÆòÀ¸·Î ÀÛ¿ëÇÏ¿© ¼ºÇüÇϰí, ±×¸² (b)¿¡¼´Â
ÀÎÀåµÈ »óÅ¿¡¼ punch°¡ ÇϰÇÏ¿© drawingÇÑ´Ù.
´ëºÎºÐÀÇ ÇÕ±ÝÀº 2 ~ 4% ¿¬½Å(æÅãß)µÇ¾úÀ» ¶§ ÀǿܷΠ¿¬¼ºÀÌ Ä¿Á®¼ ¿¬½ÅµÇÁö ¾ÊÀº »óÅ¿¡¼ÀÇ ¼ºÇü·ÂÀÇ 1/3
Á¤µµ·Î ¼ºÇüÀÌ °¡´ÉÇÏ´Ù. ÆÇÀç´Â ´ëºÎºÐ 4°¢ÇüÀ¸·Î¼ ±æÀ̹æÇâÀ¸·Î ÀÎÀåÇÏ°í Æø¹æÇâÀ¸·ÎÀÇ ¼öÃàÀ» Çã¿ëÇÑ´Ù.
dieÀÇ Àç·á´Â ºñö±Ý¼Ó, ° ¹× ¸ñÀç°¡ »ç¿ëµÇ¸ç, À±È°Á¦´Â °ÅÀÇ »ç¿ëÇÏÁö ¾Ê´Â´Ù.
ÀÎÀ强Çü¹ý¿¡¼´Â ¼ÒÀçÀÇ ÆÄ¿À» ÇÇÇÏ´Â °ÍÀÌ Áß¿äÇϸç, ¿¹¸®ÇÑ ¸ð¼¸®¸¦ °®´Â Á¦Ç°Àº °¡°øÇÒ ¼ö ¾ø´Ù.
Boeing 767ÀÇ aluminum skinµµ ÀÎÀ强Çü¹ý¿¡ ÀÇÇÏ¿© ¼ºÇüµÇ¸ç, ±× Å©±â´Â
12m¡¿2.5m¡¿2.5mmÀ̰í, ÀÎÀå·ÂÀº 9MN Á¤µµÀÌ´Ù.
ÀÎÀ强Çü¹ý ¢Ð
(9) seaming:
ÆÇ°ú ÆÇ ¶Ç´Â µ¿ÀÏ ÆÇÀÇ ¾ç´Ü(å»Ó®)À» Á¢¾î¼ ÀÕ´Â °ÍÀ¸·Î¼, °î·ü¹Ý°æÀ» ÀÛ°Ô Á¢À» ¼ö ÀÖ´Â ÆÇÀ̾î¾ß ÇÑ´Ù.
 ¿ë¾î(terms)
|