[4] drawing(±³°ú¼ p.265)
Æò¸é blank¸¦ ¿øÅëÇü(ê÷Õû¡), °¢ÅëÇü(ÊÇ÷Õû¡) ¹× ¹Ý±¸Çü(ÚâϹû¡) µîÀÇ Çü»óÀ» °®´Â
¿ë±â¸¦ ÁÖ¸§»ì ¾ø°í ÀÌÀ½¸Å ¾ø°Ô press¿¡¼ punch¿Í die¸¦ »ç¿ëÇÏ¿© ¼ºÇüÇÏ´Â °¡°øÀ» drawingÀ̶ó ÇÑ´Ù.
¿©±â¿¡¼ drawingÀ̶õ press¸¦ »ç¿ëÇÏ´Â drawing, Áï press drawingÀ» ÀǹÌÇϹǷΠ¾Õ¿¡¼ °øºÎÇÑ
¢Ñ Àιß(ìÚÚû)À̶õ ÀǹÌÀÇ drawing°ú È¥µ· ¾ø±æ ¹Ù¶õ´Ù.
¢Ñ drawing Á¦Ç°ÀÇ ¿¹·Î¼
ÁÖÀ§¿¡¼ ÈçÈ÷ º¼ ¼ö ÀÖ´Â °ÍÀ» µé¸é
³¿ºñ, ½Ä·áǰ ¿ë±â, À½·á¼ö ¿ë±â, ºÎ¾ï sink, ÀÚµ¿Â÷ ¿¬·á tank µîÀÌ ÀÖ´Ù.
¿ë±âÀÇ ±íÀ̰¡ Áö¸§º¸´Ù ÀÛÀº °æ¿ìÀÇ drawingÀ» shallow drawingÀ̶ó Çϰí, ±íÀ̰¡ Áö¸§º¸´Ù Å« °æ¿ìÀÇ
drawingÀ» deep drawingÀÌ¶ó ±¸º°ÇÏ´Â °æ¿ì°¡ ÀÖÀ¸³ª, ÀϹÝÀûÀ¸·Î ±¸º° ¾øÀÌ drawingÀ̶õ ¿ë¾î¸¦ ¸¹ÀÌ »ç¿ëÇÑ´Ù.
¿øÅëÀ» drawingÇÏ´Â °æ¿ìÀÇ ¿¹¸¦ µé¸é ¾ÐÆÇÀ¸·Î blank¸¦ ´©¸¥ »óÅ¿¡¼ punch¸¦ Çϰ½ÃŰ¸é ¼ÒÀç´Â die¿Í punch
»çÀÌ¿¡¼ ¿øÁÖ¹æÇâÀ¸·Î ¾ÐÃàµÇ°í ¹ÝÁö¸§ ¹æÇâÀ¸·Î ½Å¿¬(ãßæÅ)µÇ´Â ±Ý¼ÓÀ¯µ¿À» ÇÑ´Ù. À̶§ ¾ÐÆÇ¾Ð·ÂÀÌ ºÒÃæºÐÇϸé
flange¿¡ ÁÖ¸§ÀÌ »ý±â±â ½±°í, ¾ÐÆÇ¾Ð·ÂÀÌ ³Ê¹« Å©¸é ÆÄ¿µÉ ¼ö ÀÖ´Ù.
|
flange ÀÇ ÀÀ·Â ¢Ð
|
deep drawing¿¡¼ Áß¿äÇÑ ÀÎÀÚ´Â ÆÇ±ÝÀÇ ¼ºÁú, drawing·ü, punch¿Í dieÀÇ ¸ð¼¸® ¹ÝÁö¸§, ¾ÐÆÇ¾Ð·Â, ¸¶Âû ¹× À±È°ÀÌ´Ù.
[4-1] die¿Í punch
die¿¡´Â ¾ÐÆÇ(äã÷ù)ÀÌ ¾ø´Â ´Üµ¿½Ä die¿Í ¾ÐÆÇÀ» °®Ãá º¹µ¿½Ä die°¡ ÀÖ´Ù.
´Üµ¿½Ä die¿¡¼´Â ±×¸² (a)¿Í °°ÀÌ blank¸¦ die À§¿¡ ³õ°í punch¸¦ Çϰ½ÃŰ¸é ±×¸² (c)¿Í °°Àº ¿ë±â·Î
¼ºÇüµÇ¾î dieÀÇ ÇϴܺÎ(ù»Ó®Ý»)¿¡¼´Â springback¿¡ ÀÇÇÏ¿© punch¿Í Á¦Ç° »çÀÌ¿¡ °£±ØÀÌ »ý±â¹Ç·Î Á¦Ç°ÀÌ
¹ØÀ¸·Î ¶³¾îÁø´Ù.
-
´Üµ¿½Ä die
º¹µ¿½Ä die¿¡¼´Â ¾ÐÆÇÀÌ punchº¸´Ù ¸ÕÀú ÇϰÇÏ¿© ¼ÒÀ縦 ´©¸£°í, ´ÙÀ½¿¡ punch°¡ ÇϰÇÏ¿© drawingÀ» Çϸç,
¾Æ·¡ÀÇ ±×¸²(b)ÀÇ ¿¹¿¡¼´Â ¾ÐÆÇÀÌ 2ÁßÀ¸·Î ¼³Ä¡µÇ¾î ¿ÜÁÖÀÇ ¾ÐÆÇ°ú Áß°£ punch·Î blank¸¦ ¸¸µé°í, ±× ´ÙÀ½ Áß°£ punch°¡ ¾ÐÆÇ ¿ªÇÒÀ»
Çϰí Á߽ɿ¡ ÀÖ´Â punch°¡ ÇϰÇÏ¿© drawingÀ» ÇÑ´Ù. punch¿¡ ±¸¸ÛÀ» ³»¾î °ø±â°¡ µé¾î°¡ Á¦Ç°ÀÌ punch¿¡¼
½±°Ô ºüÁú ¼ö ÀÖ°Ô ÇÑ´Ù.
-
|
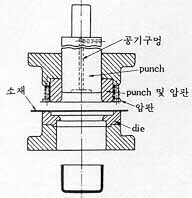 (b)
|
Áغ¹µ¿½Ä die¿¡¼´Â ±×¸²°ú °°ÀÌ punch°¡ °íÁ¤µÇ¾î ÀÖ°í die°¡ ÇϰÇϸé knock-outÀÌ »ó½ÂÇÏ¸é¼ ¾ÐÆÇÀÌ
ÇϰÇÏ¿© drawingÀÌ ÀÌ·ç¾îÁø´Ù. drawingÀÌ ¿Ï·áµÇ¾î die°¡ »ó½ÂÇϸé knock-out spring¿¡ ÀÇÇÏ¿© Á¦Ç°ÀÌ ¹Ð·Á ºüÁø´Ù.
°¡°ø Ãʱ⿡´Â ¾ÐÆÇÀÇ ¾Ð·ÂÀÌ ÀûÀ¸³ª °¡°øÀÌ ÁøÇàµÊ¿¡ µû¶ó Á¡Â÷ Áõ°¡Çϱ⠶§¹®¿¡ ±âÁؾзÂÀ» Á¤ÇϱⰡ °ï¶õÇϹǷÎ
ÁÖ·Î ¾èÀº Á¦Ç°ÀÇ drawing¿¡ ÀÌ¿ëµÈ´Ù.
-
Áغ¹µ¿½Ä die
(1) die ¹× punchÀÇ nose ¹ÝÁö¸§:
±×¸² (a)¿¡¼ dieÀÇ nose ¹ÝÁö¸§ rd¿Í punchÀÇ nose ¹ÝÁö¸§
rp°¡ Ä¿Áö¸é blankÀÇ ±ÁÈûÀúÇ×ÀÌ °¨¼ÒµÇ¾î drawingÀÌ ¿ëÀÌÇϳª,
³Ê¹« Å©¸é blank°¡ »¡¸® ²ø·Áµé¾î°¡ ¿ë±â¿¡ ÁÖ¸§ÀÌ »ý±â¸ç, ³Ê¹« ÀÛÀ¸¸é ÀÎÀ庯ÇüÀÌ Ä¿Á®¼ ¸ð¼¸®°¡
¾ã¾ÆÁö°í ÀÎÀåÀÌ ³Ê¹« ½ÉÇÏ¸é ÆÄ¿µÈ´Ù.

drawing dieÀÇ rd¿Í punchÀÇ rp°¡
drawing ·ü¿¡ ¹ÌÄ¡´Â ¿µÇâ
|
|
punch¿Í dieÀÇ ¸ð¼¸® ¹ÝÁö¸§ÀÌ
³Ê¹« ÀÛÀ» ¶§ÀÇ ÆÄ¿
(2) die¿Í punch »çÀÌÀÇ °£±Ø(ÊàÐÀ):
die¿Í punch »çÀÌÀÇ °£±ØÀº ¼ÒÀçÀÇ µÎ²² ¹× die¿Í punch »çÀÌÀÇ ¸¶ÂûÀ» ÁÙÀ̱â À§ÇÑ ¿©À¯ÀÇ ÇÕÀ̸ç,
ÀÌ ¿©À¯´Â ¼ÒÀçµÎ²²ÀÇ 7 ~ 20% Á¤µµ·Î¼ ¼ÒÀçÀÇ °µµ ¹× °¡°øÁ¤µµ¿¡ µû¶ó ´Ù¸£´Ù.
°£±ØÀÌ ³Ê¹« ÀÛÀ¸¸é Àü´Ü°¡°øÀÌ µÉ ¼ö ÀÖ°í, °£±ØÀÌ ³Ê¹« Å©¸é blank
¿Ü°æÀÇ ¾ÐÃàÀ¸·Î ÀÎÇÏ¿© rim ±ÙóÀÇ º® µÎ²²°¡ Å©°ÔµÇ´Â µî ºÒ±ÕÀÏÇÏ°Ô µÈ´Ù.
ÀÌ¿Í °°ÀÌ °£±ØÀÌ ³Ê¹« Ä¿¼ »ý±â´Â ºÒ±ÕÀÏÇÑ º® µÎ²²¸¦ Á¶Á¤Çϱâ À§ÇÏ¿© ±×¸²°ú °°ÀÌ
die¿Í punchÀÇ °£±ØÀ» drawingµÈ Á¦Ç°ÀÇ º®µÎ²²º¸´Ù ÀÛ°Ô ÃëÇÏ¿© º®ÀÇ µÎ²¨¿î ºÎºÐÀ»
¾ã°Ô ÇÏ¸é¼ ±ÕÀÏÇÏ°Ô ÇÏ´Â °¡°øÀ» ironing À̶ó Çϸç, µ¿½Ã¿¡ ³ôÀ̵µ ´Ã¾î³ª´Â redrawingÀÌ µÈ´Ù.
|
ironing
|
(3) earing:
¾Ð¿¬ÀçÀÎ ÆÇÀç´Â ¹æÇ⼺À» °®°í Àֱ⠶§¹®¿¡ deep drawingÇÏ¸é ¾Æ·¡ ±×¸²¿¡¼¿Í °°ÀÌ ¿¬½ÅÀÇ Â÷ÀÌ·Î ÆÄÇüÀÇ
´Ü¸é(Ó®Øü)À» °®°Ô µÈ´Ù. ÀÌ Çö»óÀ» ±Í¹ß»ý(ì¼Û¡ßæ; earing)À̶ó Çϸç, À̹漺(ì¶Û°àõ)ÀÌ ÀûÀº blank¸¦ »ç¿ëÇϸé
±Í(ì¼; ear)ÀÇ Å©±â´Â ÀÛ¾ÆÁø´Ù.
earing
(4) À±È°Á¦(ëÈüÁð¥; lubricant):
À±È°Á¦ÀÇ »ç¿ë¸ñÀûÀº ¸¶ÂûÀ» °¨¼Ò½Ã۰í, ¼ÒÀçÀÇ ¿ÜºÎ ¹× ³»ºÎ¿¡ ¹ß»ýÇÏ´Â ¿À» ³Ã°¢½Ã۸ç, ¼ºÇüÀ»
±ú²ýÀÌ ÇÏ°í ³ì½º´Â °ÍÀ» ¸·´Â µ¥ ÀÖ´Ù. punch¿Í blank »çÀÌ¿¡´Â ¸¶ÂûÀÌ ÀÖÀ½À¸·Î ÇØ¼ ÇÏÁßÀÌ
°ßÀκÎ(̲ìÚÝ»)¿¡ ÁýÁßµÇÁö ¾Ê°í ºÐ»êµÇ´Â È¿°ú°¡ ÀÖ¾î À¯¸®ÇϹǷΠÀ±È°Àº die¿Í blank »çÀÌ¿¡ ÇÏ´Â
°ÍÀÌ ÁÁ´Ù.
(5) blank holderÀÇ ÁöÁö·Â(ò¨ò¥Õô):
drawing Áß Á¦Ç°¿¡ ÁÖ¸§ÀÌ »ý±âÁö ¾Êµµ·Ï blank holder·Î blank¸¦ ´·¯ ÁØ´Ù. blank holderÀÇ ¾Ð·ÂÀÌ
³Ê¹« Å©¸é punchÀÇ ÇÏÁßÀÌ Ä¿Áö°í blank°¡ ÆÄ¿µÉ ¼ö ÀÖÀ¸¹Ç·Î blank holderÀÇ ¾Ð·ÂÀº Á¦Ç°¿¡ ÁÖ¸§ÀÌ »ý±âÁö
¾ÊÀ» Á¤µµÀÇ ¹üÀ§¿¡¼ ÃÖ¼Ò·Î ÇÏ´Â °ÍÀÌ ÁÁ´Ù. blank holder¿¡´Â °íÁ¤½Ä(ͳïÒãÒ)°ú Á¤¾Ð½Ä(ïÒäâãÒ)ÀÌ Àִµ¥
ÀüÀÚ¿¡¼´Â die »ó¸é°ú holderÀÇ °£°ÝÀ» ÀÏÁ¤È÷ Çϸç, °¡°øÁß ¾à°£ÀÇ ÁÖ¸§ÀÌ ¹ß»ýÇϳª punch¿Í die »çÀÌ¿¡¼
Á¦°ÅµÈ´Ù. drawingÇÒ ¶§ ÁÖ¿¬ºÎ(ñ²æÞÝ»)ÀÇ µÎ²²°¡ ¾à°£ Áõ°¡ÇϹǷΠdie »ó¸é°ú holder¿ÍÀÇ °£±ØÀº
(1.1 ~ 1.3)¡¤t Á¤µµ·Î ÇÏ´Â °ÍÀÌ ÁÁ´Ù. Á¤¾Ð½ÄÀÇ °æ¿ì¿¡´Â °í¹«, spring, À¯¾Ð, °ø±â¾Ð µîÀ¸·Î °¡°øÁß¿¡
ÀÏÁ¤ÇÑ Èû H·Î °¡¾ÐÇÑ´Ù.
(6) punchÀÇ ÀÛ¿ë·Â:
punchÀÇ ÀÛ¿ë·Â °è»ê¿¡¼ ÈçÈ÷ »ç¿ëµÇ´Â °ÍÀº blank°¡ ÆÄ¿µÇ´Â ÀÀ·ÂÀ» drawing ¾Ð·ÂÀÇ ±âÁØÀ¸·Î Çϳª,
½ÇÁ¦ÀÇ ÀÛ¿ëÀÀ·ÂÀº À̺¸´Ù ÀÛ´Ù.
±×¸²°ú °°ÀÌ ¿ë±âÀÇ Æò±ÕÁö¸§À» d, ÆÇÀÇ µÎ²²¸¦ t, blankÀÇ ÀÎÀå°µµ¸¦ ¥ò¶ó Çϸé punch ·Â P´Â
[4-2] drawing ¹æ½Ä
1Â÷ drawingÀ¸·Î ÃÖÁ¾ Á¦Ç°À» ¾ò´Â °æ¿ìµµ ÀÖ°í
Àç drawing(redrawing)ÇÏ¿© ±íÀº ¿ë±â¸¦ ¸¸µå´Â °æ¿ì¿¡ ÀüdrawingÀ» 1Â÷ drawingÀ̶ó°í ÇÑ´Ù.
´ÜÀÏ °øÁ¤¿¡¼ cup Çü»óÀÇ Á¦Ç°À» ¾ò´Â drawingÀ» cuppingÀ̶ó°íµµ Çϸç, ÀÌ ¶§ÀÇ Á¦Ç°À» cupÀ̶ó ÇÑ´Ù.
redrawing¿¡´Â ¿ë±âÀÇ ³»¿Ü¸é(Ò®èâØü)ÀÌ cupping ¶§ÀÇ °Í°ú °°Àº Á÷Á¢ redrawing(direct redrawing)°ú
cupping ¶§ÀÇ ³»¿Ü¸éÀÌ ¹Ù²î´Â ¿ª½Ä redrawing(reverse redrawing)ÀÌ ÀÖ´Ù.
±×¸² A(a)´Â cupÀ» annealingÇÏ¿© Á÷Á¢ deep drawingÀ» ÇàÇÏ´Â °ÍÀ̸ç, ±×¸² A(b)´Â ¿¬¼ÓÀûÀ¸·Î Á÷Á¢ deep drawingÀ»
ÇÏ´Â °ÍÀ» º¸¿© ÁØ´Ù. ±×¸² (B)´Â ¿ª½Ä deep drawingÀ» º¸¿©ÁÖ¸ç, ³»¿Ü¸éÀÌ ¹Ù²ñÀ¸·Î °°Àº ¸éÀÌ °è¼Ó ÀÎÀå ¶Ç´Â ¾ÐÃุÀ»
¹Þ´Â ÀÏÀÌ ¾ø´Â µî ´ÙÀ½°ú °°Àº Ư¡À» °®°í ÀÖ´Ù.
- Å« ´Ü¸é°¨¼ÒÀ²À» ¾òÀ» ¼ö ÀÖ´Ù.
- Áß°£¿¡ annealingÇÒ Çʿ䰡 ¾ø´Ù.
- º¹ÀâÇÑ Çü»ó¿¡¼µµ ±Ý¼ÓÀÇ À¯µ¿ÀÌ ÀߵȴÙ.
- µÎ²² 1/4 inº¸´Ù µÎ²¨¿î ÆÇ¿¡ ´ëÇØ¼´Â °ï¶õÇÏ´Ù.
- Á¤È®ÇÑ Á¶Á¤À» ¿äÇÑ´Ù.
|
deep drawing ¢Ð
|
[4-3] ¼ÒÀç(blank)ÀÇ Ä¡¼ö
¾Ð¿¬, ¾ÐÃâ, ÀÎ¹ß µî¿¡¼´Â ¼ÒÀçÀÇ Ã¼Àû°ú Á¦Ç°ÀÇ Ã¼ÀûÀÌ °°´Ù°í º¸°í ¼ÒÀçÀÇ Ä¡¼ö¸¦ °áÁ¤ÇÏ¿´À¸³ª,
drawing¿¡¼´Â blank¿Í Á¦Ç°ÀÇ Ç¥¸éÀûÀÌ °°´Ù°í º¸°í ¼ÒÀçÀÇ Ä¡¼ö¸¦ Á¤ÇÑ´Ù. ¾Æ·¡ Ç¥´Â º¹ÀâÇÏÁö
¾ÊÀº ¿ë±âÀÇ drawing¿¡ ÇÊ¿äÇÑ blank Ä¡¼öÀÇ ¿¹À̸ç, º¹ÀâÇÑ Çü»óÀÇ °ÍÀº ½ÇÇèÀûÀÎ
¹æ½Ä¿¡ ÀÇÇÏ¿© ±Ù»çÀûÀ¸·Î ±¸ÇÑ´Ù.
-
[4-4] drawing ·ü
deep drawing¿¡¼´Â Çʿ信 µû¶ó 1ȸ, 2ȸ µîÀ¸·Î °¡°øÇÏ¿© Á¦Ç°ÀÇ Áö¸§À» ÁÙ¿© ³ª°£´Ù. ÀÌ ¶§
blankÀÇ Áö¸§À» do,
1ȸ °¡°øÇ°ÀÇ Áö¸§À» d1,
ÃÖÁ¾ nȸ °¡°ø¿¡¼ ¾òÀº °ÍÀÇ Áö¸§À» dn¶ó Çϸé îï drawing ·ü mÀº ´ÙÀ½°ú °°´Ù.
-
Áï îï drawing ·üÀº °¢ drawing ·üÀÇ °ö°ú °°´Ù. drawing ·üÀº ÀçÁú, blank µÎ²² t/do¿¡ µû¶ó
´Ù¸£¸ç, Ç¥ (a)´Â °¢Á¾ Àç·á¿¡ ´ëÇÑ drawing ·üÀ̰í, Ç¥ (b)´Â t/do¸¦ °í·ÁÇÑ
drawing ·üÀÇ ¿¹ÀÌ´Ù.
-
[4-5] °¡°ø°æÈ(Ê¥ÍïÌãûù; work hardening)
drawing ±íÀ̰¡ Á¡Á¡ Ä¿Áö°í drawing Ƚ¼ö°¡ ¸¹¾ÆÁü¿¡ µû¶ó °¡°øÀç·á´Â ¼ÒÀ§
¢Ñ °¡°ø°æÈµÇ¾î
¼Ò¼ºº¯ÇüÀÌ ¾î·Æ°Ô µÇ¸ç, ÀÜ·ùÀÀ·ÂÀÌ Ä¿Áø´Ù. ÀÌ·± »óÅ¿¡¼ °è¼Ó ¹«¸®ÇÑ °¡°øÀ» ÇÏ¸é °¡°øÀç·á°¡ ÆÄ¿µÇ¹Ç·Î
¢Ñ Ç®¸²(annealing)ÇÏ¿©
¼Ò¼ºÀ» ȸº¹½ÃÄÑ ÁÖ¾î¾ß ÇÑ´Ù.
Àç·áÀÇ °¡°ø°æÈ¼ºÀº Àç·á¿Í °¡°øÁ¤µµ ¹× °¡°øÁ¶°Ç¿¡ µû¶ó ´Ù¸£³ª, ³Ã°£ drawing¿¡¼´Â ´ÙÀ½ °¡°ø°æÈ°î¼±À»
ÀÌ¿ëÇϰí ÀÖ´Ù. °¢ °î¼±ÀÇ ¾Æ·¡ ºÎºÐ¿¡¼´Â °¡°øÀç·á°¡ ¿¬Áú»óÅÂÀ̰í, À§ ºÎºÐ¿¡¼´Â °æÁú»óÅÂÀÌ´Ù. °î¼±ÀÇ ±â¿ï±â´Â
°¡°ø°æÈÀ²ÀÇ Ã´µµ·Î¼ ±â¿ï±â°¡ Ŭ¼ö·Ï °æÈ¼Óµµ°¡ Å« °ÍÀÌ µÈ´Ù.
-
°¡°ø°æÈ°î¼±
¾Æ·¡ ±×¸²Àº ÃÖÀú»ç¿ëÇ׺¹Á¡ ¥ò©û = 48,000 lb/in©÷,
ÃÖ°í»ç¿ëÇ׺¹Á¡ ¥ò©ü = 92,000 lb/in©÷ÀÎ Àç·á¿¡
´ëÇÑ °¡°ø°æÈ°î¼±ÀÌ´Ù. ¿¹·Î¼ 1Â÷ °¡°ø¿¡¼ 40%, 2Â÷ °¡°ø¿¡¼ 30%ÀÇ ´Ü¸é°¨¼ÒÀ²·Î Çϸé
îï´Ü¸é°¨¼ÒÀ²Àº
-

ÀÌ´Ù.
À§ ¿¹Á¦ÀÇ °è»ê ´ë½Å¿¡ graph¿¡¼ îï´Ü¸é°¨¼ÒÀ²°ú °¡°øÀÀ·ÂÀ» ±¸ÇØ º¸±â·Î ÇÑ´Ù.
°æÈ°î¼±»óÀÇ ¥ò©ý¿Í x Ãà¿¡¼ÀÇ ´Ü¸é°¨¼ÒÀ²À» ³ªÅ¸³»´Â Á¡µé°ú ÀÖ°í, ¥ò©û Á¡¿¡¼ x Ãà¿¡ ÆòÇàÇÏ°Ô ±×¾î
´Ü¸é°¨¼ÒÀ² 40%ÀÇ ¼±°úÀÇ ±³Á¡¿¡¼ y Ãà¿¡ ÆòÇ༱À» ±×¾î 1Â÷°¡°ø¿¡¼ÀÇ ÀÀ·ÂÀ» ±¸ÇÑ´Ù. 1Â÷°¡°øÀÀ·ÂÁ¡¿¡¼
x Ãà¿¡ ÆòÇàÇÏ°Ô ´Ü¸é°¨¼ÒÀ² 30%ÀÇ ¼±°úÀÇ ±³Á¡¿¡¼ ¼öÁ÷¼±À» ¿Ã·Á 2Â÷°¡°ø¿¡¼ÀÇ °¡°øÀÀ·Â
¥ò= 83,000 lb/in©÷¸¦ ±¸ÇÒ ¼ö ÀÖ´Ù.
2Â÷°¡°ø ÈÄ ÀÀ·ÂÀÌ ÃÖ°í¹üÀ§¿¡ Á¢±ÙÇϹǷΠǮ¸²Ã³¸®¸¦ ÇÏ¿© 3Â÷°¡°ø ¹× ±× ÀÌ»óÀÇ °¡°øÀ» ÇÏ´Â °ÍÀÌ ÁÁ´Ù.
-
°¡°ø°æÈ°î¼±ÀÇ »ç¿ë¿¹
|