[3] ¶ìÅé±â°è(bandsawing machine, bandsaw)(±³°ú¼ p.443)
±×¸²°ú °°ÀÌ pulleyÀÇ È¸Àü¿îµ¿¿¡ ÀÇÇÏ¿© ¶ìÅéÀ» ¿îµ¿½ÃÄÑ Àý´ÜÀÛ¾÷À» ÇÏ´Â ±â°è¸¦ ¶ìÅé±â°è(band sawing machine)À̶ó
Çϸç, ¶ìÅéÀÇ Àý´Ü¿îµ¿ ¹æÇâ¿¡ µû¶ó ¼öÆò½Ä°ú ¼öÁ÷½ÄÀÌ ÀÖ´Ù.
±Ý¼ÓÀý´Ü¿ë ¶ìÅ鳯(bandsaw blade)ÀÇ Àç·á, Ä¡Çü»ó ¹× Ä¡ÀÇ ¹è¿Àº ȰÅ鳯(hacksaw blade)¿¡¼¿Í °°´Ù.
Á¤¹ÐÇÑ Á÷¼±À¸·Î Àý´ÜÇϱâ À§ÇÏ¿©´Â ÆøÀÌ ³ÐÀº ¶ìÅ鳯À» »ç¿ëÇϰí, °î·ü¹ÝÁö¸§ÀÌ ÀÛÀº °î¼±Àý´ÜÀ» À§Çؼ´Â
Á¼Àº ÆøÀÇ ¶ìÅ鳯À» »ç¿ëÇÑ´Ù. µÎ²¨¿î Àç·áÀÇ Àý´Ü¿¡¼´Â pitch°¡ Å« ¶ìÅ鳯À» »ç¿ëÇÏ°í ¾ãÀº Àç·áÀÇ
Àý´Ü¿¡¼´Â ÀÛÀº pitchÀÇ Å鳯À» »ç¿ëÇÑ´Ù. ±âº»ÀûÀ¸·Î Àû¾îµµ 2°³ ÀÌ»óÀÇ ÀÌ(öÍ)°¡ µ¿½Ã¿¡
°¡°øÀç·á¿Í ¹°¸®°í ÀÖ¾î¾ß ÇÑ´Ù. ¶ìÅ鳯ÀÇ µÎ²²´Â Å鳯ÀÇ Æø¿¡ µû¶ó Ç¥ÁØÈ µÇ¾î ÀÖ´Ù.
Æø 1/2in ±îÁö´Â µÎ²²°¡ 0.025in, Æø 5/8in¿Í 3/4in¿¡ ´ëÇÏ¿©´Â 0.032in, Æø 1in¿¡ ´ëÇÏ¿©´Â 0.035inÀÇ
µÎ²²·Î µÇ¾î ÀÖ´Ù. µÎ²¨¿î Å鳯Àº °µµ°¡ Å©¹Ç·Î °ÀÎÇÑ(tough) Àç·áÀÇ Àý´Ü¿¡ »ç¿ëµÈ´Ù.
¶ìÅ鳯Àº ÀϹÝÀûÀ¸·Î coil ÇüÅ·ΠµÇ¾î ÀÖ¾î Åé±â°è¿¡ µû¶ó ÇÊ¿äÇÑ ±æÀ̸¸Å Àý´ÜÇÏ¿©
¾ç³¡À» ¸Â´ë°í ¿ëÁ¢ÇÏ¿© »ç¿ëÇÑ´Ù.
(1) ¼öÆò½Ä ¶ìÅé±â°è(horizontal bandsawing machine):
¼öÆò½Ä bandsawing machine¿¡¼´Â belt Çü»óÀÇ ¾ãÀº Å鳯(blade)ÀÌ ÁÂ¿ì ¶Ç´Â ¼öÆòÀ¸·Î À§Ä¡ÇÑ
pulleyÀÇ È¸Àü¿îµ¿¿¡ ÀÇÇÏ¿© ÇÑÂÊ ¹æÇâÀ¸·Î ¿¬¼Ó¿îµ¿À» ÇÏ¸é¼ Àý´ÜÀÛ¾÷À» ¼öÇàÇÑ´Ù.
roller guide°¡ Å鳯À» Ʋ¾î ¼öÁ÷À¸·Î À§Ä¡½Ã۰í, pulley Ãà¹æÇâÀ¸·ÎÀÇ À̵¿À» ¹æÁöÇϸç,
Å鳯À» 450kg Á¤µµ±îÁö ÀÎÀåÇÏ¿© Å鳯¿¡ Àû´çÇÑ °¼ºÀ» ÁØ´Ù.
¼öÆò½Ä ¶ìÅé±â°è´Â Àý»è¼Óµµ°¡ 20~150m/min Á¤µµ·Î Å©°í °¡°ø¹°ÀÇ °íÁ¤ÀÌ ¿ëÀÌÇϸç
scrap ¼Õ½ÇÀÌ ÀûÀº µîÀÇ ÀåÁ¡À» °®°í ÀÖ¾î ³Î¸® »ç¿ëµÃ´Ù.
¼öÆò½Ä bandsawing machine ¢Ð
|
¶ìÅ鳯
|
¼öÆò½Ä bandsawing machine¿¡¼ Àý´Ü°¡°øÀ» ÇÑ´Ù.
(7.37MB/2.2min)
|
¼öÆò½Ä bandsawing machine¿¡¼ Àý´Ü°¡°øÀ» ÇÑ´Ù.
|
(1) ¼öÁ÷½Ä ¶ìÅé±â°è(vertical bandsawing machine, counter bandsawing machine):
»óÇÏ¿¡ À§Ä¡ÇÑ pulleyÀÇ È¸Àü¿îµ¿¿¡ ÀÇÇÏ¿© ¶ìÅ鳯(band blade)ÀÌ ¿¬¼ÓÀûÀ¸·Î ¼öÁ÷ Àý»è¿îµ¿À» Çϰí
table»ó¿¡¼ °¡°ø¹°¿¡ À̼ÛÀ» ÇÏÇÔÀ¸·Î½á Àý´ÜÀÛ¾÷À» Çϸç, tableÀ» °æ»ç½ÃÄÑ °æ»çÀý´Ü ¹× °æ»ç°¡°øÀ» ÇÑ´Ù.
ÅéÀÛ¾÷¿Ü¿¡ ´Ù¾çÇÑ ºÎ¼ÓÀåÄ¡ ¹× °ø±¸¸¦ ¼³Ä¡ÇÏ¿© »çÆ÷ÀÛ¾÷, polishing ¹× ¸¶ÂûÀý´Ü µîÀ» ÇÒ ¼ö ÀÖ´Ù.
¼öÁ÷½ÄÀº Àý´ÜÀÛ¾÷°ú À±°ûÀÛ¾÷(ëÌΩíÂåö)À» ÇÒ ¼ö ÀÖ°í À±°ûÀÛ¾÷Àº °¡°ø¹°À» table¿¡¼ ¿òÁ÷¿© ÇàÇÑ´Ù.
¼öÁ÷½Ä ¶ìÅ鳯(bandsaw blade)¿¡´Â ¿ëµµ¿¡ µû¶ó ´ÙÀ½ ±×¸²(a)¿Í °°ÀÌ ¿©·¯ Á¾·ù°¡ ÀÖ°í,
1 in ´ç 2 ~ 32°³ÀÇ Åé´Ï¸¦ °®´Â pitch·Î µÇ¾î ÀÖ´Ù. À±°û°¡°ø¿¡¼´Â Àý´Ü°î¼±ÀÇ
°î·ü¹ÝÁö¸§¿¡ µû¶ó ÅéÀÇ ÆøÀÌ ´Ù¸£¸ç, ±×¸²(b)´Â ÅéÀÇ Æø¿¡ µû¸¥ °¡°øÇÒ ¼ö ÀÖ´Â
ÃÖ¼Ò °î·ü¹ÝÁö¸§À» Ç¥½ÃÇÑ °ÍÀÌ´Ù.
Àý»è¼Óµµ´Â °¡°øÀç·á, Å鳯Àç·á ¹× °¡°øºÎÀÇ Å©±â µî¿¡ µû¶ó ´Ù¸£³ª
¢Ñ °í¼Óµµ°(ÍÔáÜÓøË¼; high speed steel, H.S.S.)
Å鳯¿¡ ÀÇÇÑ Àý´Ü¿¡¼ °¡°øÀç·á°¡ º¸Åë°ÀÏ ¶§ 50 ~ 80m/min, ±¸Á¶¿ë°ÀÏ ¶§ 20 ~ 45m/min,
ÁÖöÀÏ ¶§ 25 ~ 65m/min, ÁÖ°ÀÏ ¶§ 25 ~ 70m/min Á¤µµÀÌ´Ù.
¼öÁ÷½Ä band sawing machine ¢Ð
|
¼öÁ÷½Ä band sawing machine¿¡¼ °¡°ø¹°ÀÇ À̼۹æÇâÀ» Á¤ÇÏ´Â guide¸¦ »ç¿ëÇÑ´Ù.
|
-
¶ìÅéÀÇ Á¾·ù ¹× ¶ìÅ鳯 Æø
-
¼öÁ÷½Ä ¶ìÅé¿¡¼ÀÇ °¢Á¾ ÀÛ¾÷
-
Àý»è¼Óµµ´Â ¶ìÅé±â°è, ¶ìÅé , Àý»èÀ¯Á¦, Àý»è±íÀÌ, ¹× °¡°ø¹°ÀÇ ¼ºÁú°ú µÎ²² µîÀÇ Á¶°Ç¿¡ µû¶ó ´Ù¸£´Ù.
¶ìÅéÀÇ butt ¿ëÁ¢Àº ´ë´ÜÈ÷ Áß¿äÇÑ °ÍÀ¸·Î¼, Åé±â°è¿¡ ¿ëÁ¢±â°¡ ¼³Ä¡µÈ °Íµµ ÀÖ°í, ¿ëÁ¢¿ÀÌ ½Ä±â Àü¿¡
Ç®¸²(annealing)󸮱îÁö ÇÑ´Ù.
Àý»è°¡°øÆíÀÇ ±â°èÅé °¡°øÀ» ±â¼úÇÏ´Â ¹üÀ§¿¡ ¿¬»èÀý´Ü(æÚÞûï·Ó¨), ¸¶ÂûÀý´Ü(ؤóÍï·Ó¨),
¹× ¼ö·ùÀý´Ü(â©×µï·Ó¨)À» Æ÷ÇÔ½ÃŰ´Â °ÍÀº º» ±³ÀçÀÇ ºÐ·ù»ó ´Ù¼Ò ¾î»öÇÑ °¨ÀÌ ÀÖÀ¸³ª,
Àý´ÜÀ̶ó´Â °øÅëÁ¡ÀÌ Àֱ⠶§¹®¿¡ ÀÌ¾î¼ ±â¼úÇϱâ·Î ÇÑ´Ù.
[4] ¿¬»èÀý´Ü
°áÇÕÁ¦·Î ÇÕ¼º¼öÁö µîÀ» »ç¿ëÇÑ ¾ãÀº ¿¬»è¼ýµ¹·Î ±Ý¼Ó ¹× ºñ±Ý¼ÓÀ» Àý´ÜÇϸç, ºÀ(Üê)Àº Áö¸§ 50mm Á¤µµ±îÁö,
°ü(η)Àº Áö¸§ 90mm Á¤µµ±îÁö Àý´ÜÇÒ ¼ö ÀÖ´Ù. Àý»è¼Óµµ(¿øÁÖ¼Óµµ)´Â 5000m/min ±îÁö ÃëÇÒ ¼ö ÀÖ¾î
¹ß»ý¿ÀÌ ³Ã°¢µÇ±â Àü¿¡ Àý´ÜÇϱ⠶§¹®¿¡ Àý´Ü¼Óµµ°¡ Å©´Ù. ¼ýµ¹À» º¸È£Çϱâ À§ÇÏ¿© ¿¬»èÀ¯Á¦¸¦ °ø±ÞÇÒ ¶§´Â
Àý´ÜÀÛ¾÷ÀÌ ¿·Î ÀÎÇÑ ¿¬È¿¡ ÀÇÇÑ °ÍÀÌ ¾Æ´Ï°í, Àý»èÀÛ¿ë¿¡ ÀÇÇÑ °ÍÀÌ µÇ¸ç Àý»è¼Óµµ´Â 2500mm/min Á¤µµ·Î
ÇÑ´Ù.
-
¢Ð
|
|
[5] ¸¶ÂûÀý´Ü
¸¶ÂûÀý´ÜÀº Å鳯°ú °¡°ø¹°ÀÇ ¸¶Âû¿¿¡ ÀÇÇÏ¿© °¡°ø¹°ÀÇ Á¢Ã˺ΰ¡ ¿¬È(æãûù)µÇ°í »êÈµÈ »óÅÂÀÇ
±Ý¼ÓÀ» ¹Ð¾î³¿À¸·Î½á ¼öÇàµÇ¸ç, Àý´Ü¼Óµµ°¡ ¾î´À Àý»èÀý´Ü¿¡¼ º¸´Ù Å©°í Àý´Ü¸éµµ ´Ù¼ÒÀÇ
burr°¡ ÀÖÀ¸³ª ºñ±³Àû ¸Å²öÇÏ´Ù.
ÅéÀÇ ¼Óµµ¸¦ 500m/min Á¤µµ·Î ¾ÆÁÖ Å©°ÔÇÏ¿© ªÀº ½Ã°£¿¡ ¿À» ¸¹ÀÌ ¹ß»ý½ÃÅ´À¸·Î½á °¡°ø¹°ÀÌ
¹ß»ý¿À» ÀüµµÇÏ¿© Èí¼öÇϱâ Àü¿¡ Àý´ÜµÇ´Â Á¶°ÇÀÌ ÇÊ¿äÇÏ´Ù.
Å鳯À» º¸È£Çϱâ À§ÇÏ¿© Å鳯ÀÌ ±ä ¿øÁÖÅé±â°è ¶Ç´Â ¶ìÅé±â°è°¡ »ç¿ëµÇ¸ç, ¸¶ÂûÀý´Ü¿¡
»ç¿ëµÇ´Â Å鳯Àº Ç¥ÁØÅº¼ÒÇձݰÀ¸·Î¼ Àý»èÀý´Ü Å鳯¿¡ ºñÇÏ¿© µÎ²®°ÔÇÔÀ¸·Î½á °µµ¸¦ Å©°Ô Çϰí ÀÖ´Ù.
¸¶ÂûÀý´ÜÀº ¿Àüµµµµ°¡ »ó´ëÀûÀ¸·Î ³·Àº ö±Ý¼ÓÀÇ Àý´Ü¿¡ À¯¸®Çϸç 25mm Á¤µµÀÇ µÎ²²±îÁö Àý´ÜÀÌ °¡´ÉÇÏ´Ù.
ƯÈ÷ °¡°ø°æÈ ¶§¹®¿¡ Àý»èÀý´ÜÀÌ ¾î·Á¿î stainless °°ú °æµµ°¡ Å« öÇÕ±Ý µîÀÇ Àý´Ü¿¡¼ ´õ¿í À¯¸®Çϸç,
°¡°ø´É·üÀº °¡°ø¹°ÀÇ °æµµ¿Í´Â ¹«°üÇÏ´Ù. ¹Ý¸é¿¡ Àý´ÜµÇ±â Àü¿¡ ±Ý¼ÓÀÔÀÚ°¡ ÆÄ±«µÇ´Â ÁÖö,
¿Àüµµµµ°¡ Å« aluminum°ú Ȳµ¿ µîÀº ¿ÀÌ ±¹ºÎÀûÀ¸·Î ÁýÁßµÇ±â ¾î·Æ°í °¡°ø Áß Å鳯¿¡ ´Ã¾îºÙ´Â
¼ºÁú ¶§¹®¿¡ ¸¶ÂûÀý´Ü¿¡ ºÎÀû´çÇÏ´Ù.
¸¶ÂûÅéÀý´Ü¿¡´Â ¿øÆÇ¸¶ÂûÀü´Ü(circular friction sawing)°ú ¶ì¸¶ÂûÀý´Ü(friction bandsawing)ÀÌ ÀÖÀ¸¸ç,
¿øÆÇ¸¶ÂûÀü´ÜÀº ¿øÁÖÅé±â°è¿¡¼ ÇàÇØÁö°í ¶ì¸¶ÂûÀý´ÜÀº ¶ìÅé±â°è¿¡¼ ÇàÇØÁø´Ù.
¿øÆÇ¸¶ÂûÅ鳯Àº ÆøÀÌ 12.7mm, 19.5mm, 25.4mmÀ̰í, raker set¿¡¼ pitch°¡ 10»ê/in ¹× 14»ê/in À̸ç, ³¯À»
¿¹¸®ÇϰÔÇÏ´Â ¿¬»èÀº ÇÏÁö ¾Ê´Â´Ù. Àý´ÜÀÛ¾÷½Ã¿¡ ÀÛ¾÷ÀÚ¸¦ º¸È£Çϱâ À§ÇÑ º¸È£¸·ÀÌ ÇÊ¿äÇÏ´Ù.
-
¿øÆÇ¸¶ÂûÅé (Áö¸§ 1000mm ~ 2400mm)
¢Ð
|
peg tooth(standard profile)
peg tooth with land(for cutting steel tube)
XLR tooth(for cutting jumbo beam)
handsaw tooth(for cutting solid bar and billets)
skip tooth(for cutting jumbo beam)
ÅéÀÌÀÇ Çü»ó
|
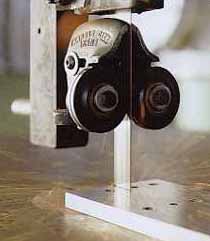
bandsawing machine¿¡¼ ¸¶ÂûÀý´Ü
|
[6]¼ö·ùÀý´Ü(â©×µï·Ó¨; waterjet cutting)
¿¬¸¶ÀÔÀÚ¸¦ ÷°¡ÇÑ ¹°À» nozzle¸¦ ÅëÇÏ¿© °¡°ø¹°¿¡ µû¶ó ´Ù¸£³ª ¾Ð·Â 4200kg/§² Á¤µµ,
¼Óµµ 28km/min Á¤µµ·Î ºÐ»çÇÏ¿© Àý´ÜÇÏ´Â °ÍÀ» ¼ö·ùÀý´ÜÀ̶ó Çϸç, À¯¸®¿¡¼ °í°µµÇձݿ¡
À̸£±â±îÁö ±Ý¼ÓÀç·á ¹× ºñ±Ý¼ÓÀ縦 ¸Á¶óÇÏ¿© °ÅÀÇ ¸ðµç Àç·á¸¦ µÎ²² 250mm Á¤µµ±îÁö Àý´ÜÇÒ ¼ö ÀÖ´Ù.
Àý´Ü¸éÀº »çÆ÷ÁúÇÑ °Íó·³ º¸ÀδÙ. ¿¬¸¶ÀÔÀÚ°¡ ¼ö·ùÀý´Ü ºñ¿ëÀÇ 60 ~ 65%¸¦ Â÷ÁöÇϱâ
¶§¹®¿¡ ÃÖ±Ù¿¡´Â ¾Ð·ÂÀ» ³ô°Ô ÇÏ¿© »ç¿ëÇÔÀ¸·Î½á ¿¬¸¶ÀÔÀÚ ¾ø´Â ¼ö·ùÀý´ÜÀ» ½ÃµµÇϰí ÀÖ´Ù.
-
¢Ð waterjet¿¡ ÀÇÇÑ Àý´Ü
|
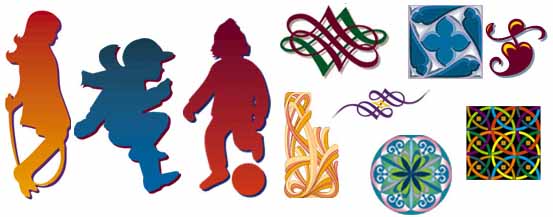
¼ö·ùÀý´Ü ¿¹
|
¼ö·ùÀý´Ü¹ýÀÇ ÀåÁ¡À» µé¸é ´ÙÀ½°ú °°´Ù.
- Àý´Ü¸éÀÇ ¿Âµµ°¡ 20¡É Á¤µµ·Î ³·±â ¶§¹®¿¡ ¿º¯ÇüÀ» Æ÷ÇÔÇÑ ¿¿µÇâºÎ°¡ ¹ß»ýÇÏÁö ¾Ê´Â´Ù.
- ºÐ»ç¹æÇâÀ» ÀÓÀÇ·Î Á¶Á¤ÇÒ ¼ö Àֱ⠶§¹®¿¡ ÀÓÀÇ °¢µµ·Î Àý´ÜÇÒ ¼ö ÀÖÀ¸¸ç, º¹ÀâÇÑ °î¼±ÀÇ Àý´ÜÀÌ °¡´ÉÇÏ´Ù.
- ºÐ·ùÀÇ Áö¸§ÀÌ 0.7 ~ 1.5mm Á¤µµÀ̹ǷΠÀý´Ü¿¡ ÀÇÇÑ Àç·á ¼Õ½ÇÀÌ Àû´Ù.
- 1ȸÀÇ Åë°ú·Î Àý´ÜÀÌ ¿Ï·áµÇ¸ç, Àý´Ü¼Óµµ°¡ ÀüÅëÀûÀÎ ¹æ¹ý¿¡¼ º¸´Ù Å©´Ù.
- burr°¡ °ÅÀÇ ¾ø°í Ä¡¼ö¿Í Àý´Ü¸éÀÇ Ç¥¸éÁ¤µµ°¡ ³ô¾Æ 2Â÷°¡°øÀÌ ÇÊ¿ä¾ø´Ù.
|